What's the Difference Between PVD and CVD Coating Processes?


Physical Vapor Deposition (PVD) and Chemical Vapor Deposition (CVD) are two “families” of processes commonly used to produce thin films on a variety of substrates. These films (typically less than 100µm, ~4 mil) can add mechanical, optical, chemical, and/or electronic properties to the coated material. As such, they are used across different industries, including automotive, cutting tools, precision components, home hardware, medical devices, molds & dies, firearms, and blades, among others.
PVD and CVD coating processes
Both PVD and CVD convert a vapor of some substance into a solid coating on the surface of a substrate (tool or part). However, they differ in how the process occurs. PVD involves removing atoms, molecules, and ions from a solid source (target) and condensing them onto the substrate. CVD uses vaporized liquids or gases as sources that chemically react on or close to the surface of the substrate to form a solid film. While PVD processes always occur in a vacuum, CVD can occur at high vacuum to atmospheric pressure.
The PVD coating process includes removing material from a target via evaporation or sputtering. Evaporation can be achieved using different forms of energy, such as cathodic arc, direct heating-thermal, electron beam, and laser beam. Sputtering, on the other hand, employs the bombardment of a target by ionized gas(es), which removes atoms and molecules by momentum transfer. Among PVD methods, cathodic arc evaporation (CAE) and sputtering are the more widely commercially used processes. Some examples of coatings produced by PVD include pure metals and compounds such as TiN, ZrN, CrN, TiCN, TiAlN, CrAlN, and ZrOC.
CVD methods include APCVD (atmospheric pressure CVD), LPCVD (Low-pressure CVD – thermal), APCVD (atmospheric pressure CVD), LPCVD (Low-pressure CVD – thermal), and PECVD (plasma enhanced CVD).
- The plasma-enhanced CVD coating process relies on a low-pressure plasma to activate the vapor or gas, allowing substrates to be coated at much lower temperatures than thermal processes. VaporTech DLC coatings are applied using PECVD. PECVD can produce a-C:H DLC, electronic grade silicon, SiNx, and SiO.
- On the other hand, non-plasma CVD processes employ thermal energy to enable the chemical reactions that form the coating. Because of the high temperatures required, there are limitations to the substrate materials that can be used. Examples of coatings produced by thermal CVD include Si3N4, SiC, Al2O3, TiN, and TiCN.
Although some coatings, e.g. TiN and TiCN, can be produced by both CVD and PVD coating processes, the temperatures involved in each process are notably different. In VaporTech equipment, PVD can produce TiN and TiCN at temperatures under 200oC. CVD requires temperatures around 1000oC. Many substrate materials can’t stand up to those temperatures, thus limiting this process’ use.
VaporTech PVD & DLC systems
For more information about VaporTech PVD and PECVD equipment (both can be used in the same chamber), please contact us today at 303.652.8500.
Recent posts
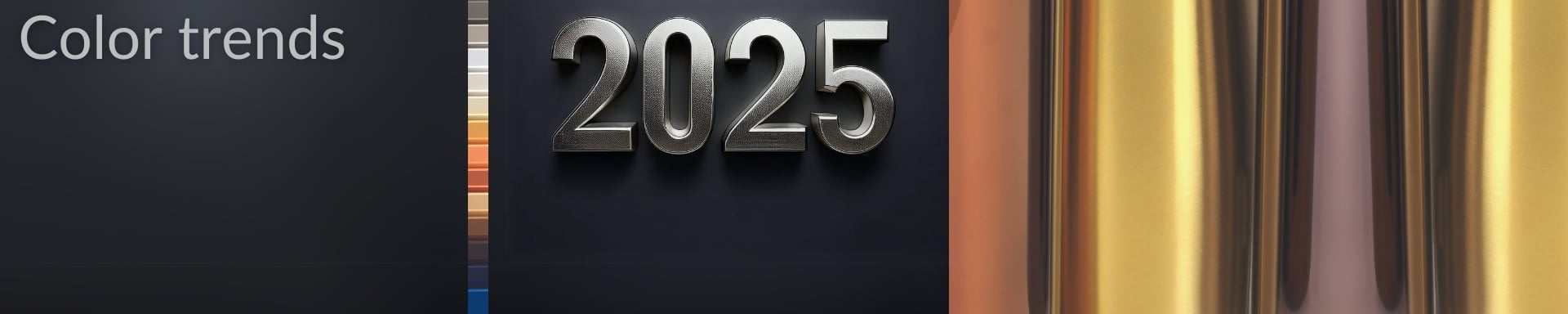
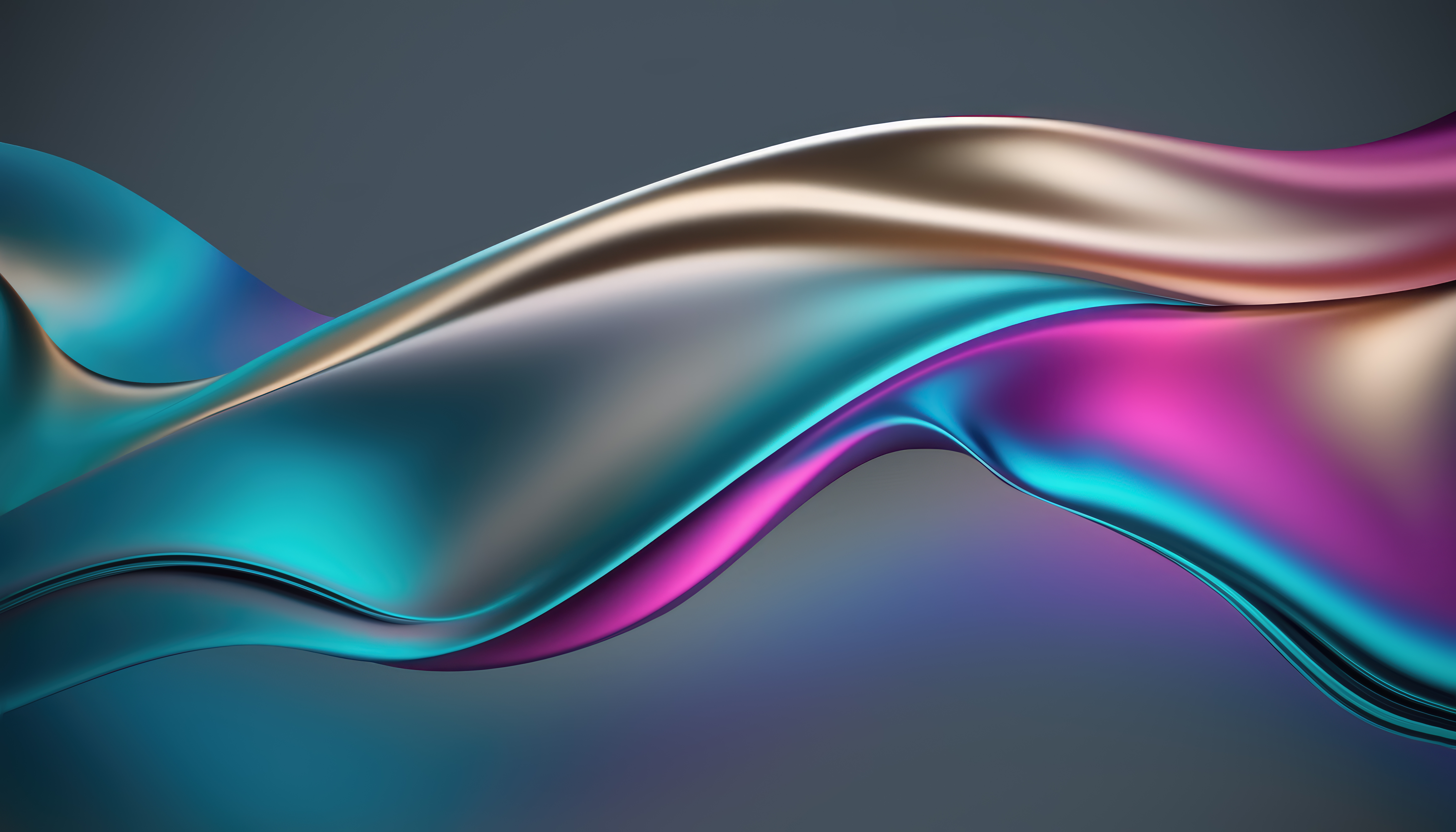
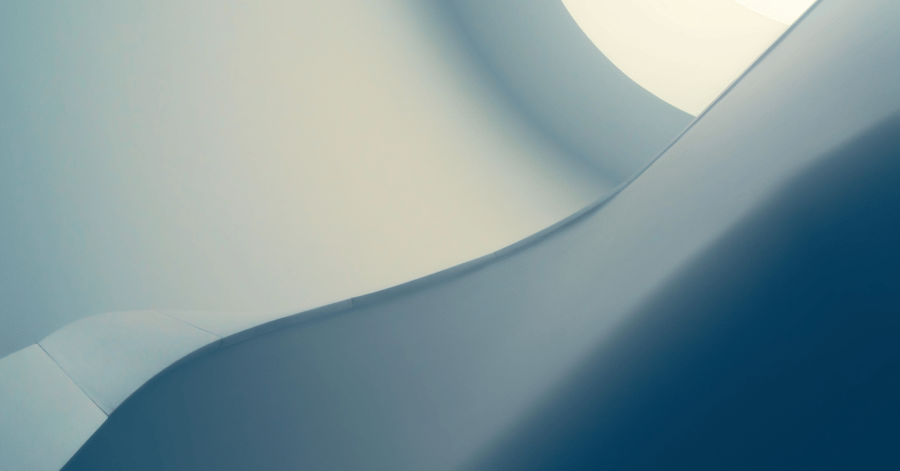
What is PECVD? Use it to Create DLC coatings in Your Vapor Deposition System.
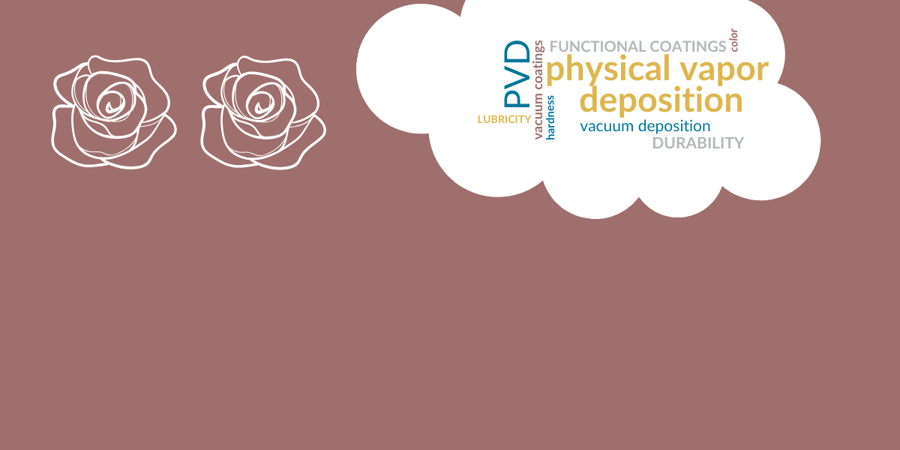