3 Compact PVD Coating Systems That Deliver Big Results [updated]


- VaporTech's VT i series offers compact, right-sized PVD coating systems designed for small to medium-sized operations, providing high-quality coatings with a smaller footprint and enhanced affordability.
- Bringing PVD coating in-house with these systems can speed up production, reduce defects, lower shipping costs, and allow for customized finishes tailored to specific product specifications.
- The VT-1000i, VT-1500i, and VT-3000i models cater to varying production volumes, offering flexibility and scalability to meet diverse manufacturing needs.
Benefits of In-House PVD Coating Equipment
VaporTech President Dave Humenik: Speed production, reduce defects, avoid repackaging, reduce shipping costs, and customize your finishes with the same compact PVD coating systems used by manufacturers worldwide.
Manufacturers have known the benefits of in-house PVD* coating for decades: time savings, quality control, and customized thin-film coatings that differentiate products by improving function and appearance. However, in the past, capital investment was too high for lower-volume operations, the machines were too large or complex to integrate into existing manufacturing facilities, and the industry perceived that these machines required highly trained specialists to operate and maintain.
*Although we (and the industry) refer to these as “PVD Coatings,” PVD (physical vapor deposition) is only one of several processes that are used in thin-film deposition systems. Chemical vapor deposition (CVD) is another process of applying thin-film coatings, including diamond-like carbon (DLC). All our VaporTech vacuum coating machines deposit nanometers-thick metal or ceramic coatings to various metal or plastic parts. They are fade-resistant, uniform, and, in many applications, can outperform other coating technologies. But before I introduce our new VT-Series products, all compact PVD and PECVD/DLC coating systems, I will provide some background for those who are new to the idea of PVD coatings or applying these coatings in-house.
Why choose PVD coatings?
Manufacturers benefit from thin-film deposition as these coatings can improve the durability, function, and aesthetics of a broad range of metal (and some plastic) parts. Our systems produce extremely thin, hard, durable metallic and diamond-like-carbon coatings. In addition, our decorative hard coatings are available in a broad range of metallic colors. The unique VaporTech® chamber design can also operate at lower temperatures, giving companies the ability to coat temperature-sensitive parts–examples include zinc die-cast components and even some plastics. Industries we serve include:
- Automotive
- Medical device
- Architetural hardware
- Sporting goods/Outdoor sports
- Luxury items
- Consumer products
Why bring PVD coating in-house?
The new VaporTech® right-sized coating systems are designed to simplify the process of bringing PVD into your manufacturing operation. A smaller footprint, easy loading/unloading of parts, straightforward routine maintenance, and a simple coating-recipe-based interface make the system well matched to a broader range of applications. If your company is currently shipping products out for coating, bringing the PVD coating process in-house allows your company to speed production, reduce defects, avoid repackaging, reduce shipping costs, and provide the ability to customize a finish to your product specifications rather than use an “off-the-shelf” process.
So what’s different about our new series of coaters?
We’ve been developing PVD coating equipment for decades, and our new VT-1000i™, VT-1500i™, VT-3000i™ coating systems are now installed at manufacturing facilities around the world. Based on feedback from our customers we have now introduced systems that:
- Are right-sized for all operations
- Are affordable
- Have a much smaller footprint
- Are easy to operate
- Provide the same high-quality coatings as their industrial counterparts.
Introducing the new VTi series of right-sized compact PVD coating systems
The new VT-1000i system is a compact, higher-capacity offering for small-to-medium-sized operations. It’s a PVD and DLC system designed for low-to-higher volume applications, and more parts per batch mean a lower cost per part and faster return on your investment. This machine coats large parts up to 100 cm long. For more information:
For higher volume or quickly growing operations, the VT-1500i system may be an excellent fit. This system provides approximately 70% of the throughput of our largest production coating system but in a very compact footprint when manufacturing space is limited. With the ability to coat parts up to 100 cm long and 10 high-capacity racks, the VT-1500i is positioned as a high-volume, price-competitive coating system for larger manufacturing operations.
The VT-3000i coating system is our highest capacity machine now available in a small footprint for easier integration and savings. For more information: Email sales.
Recent posts
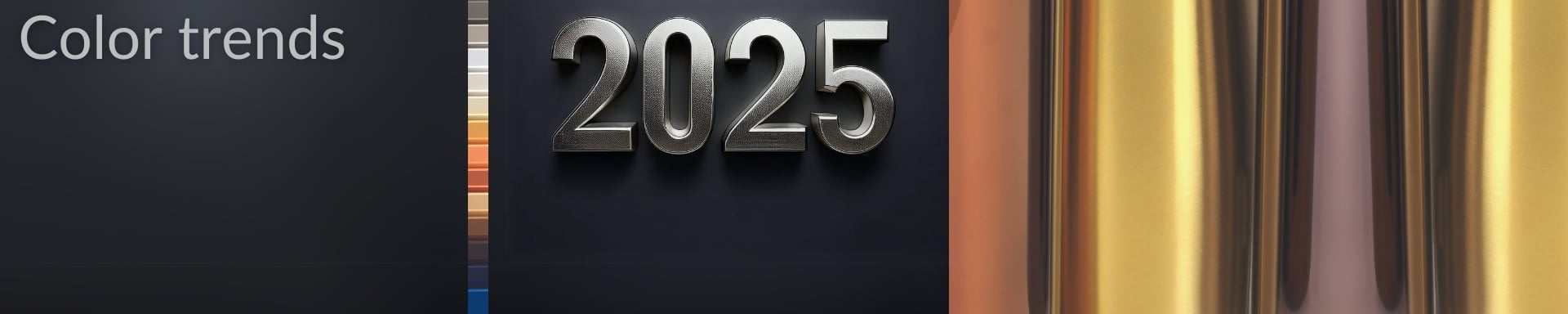
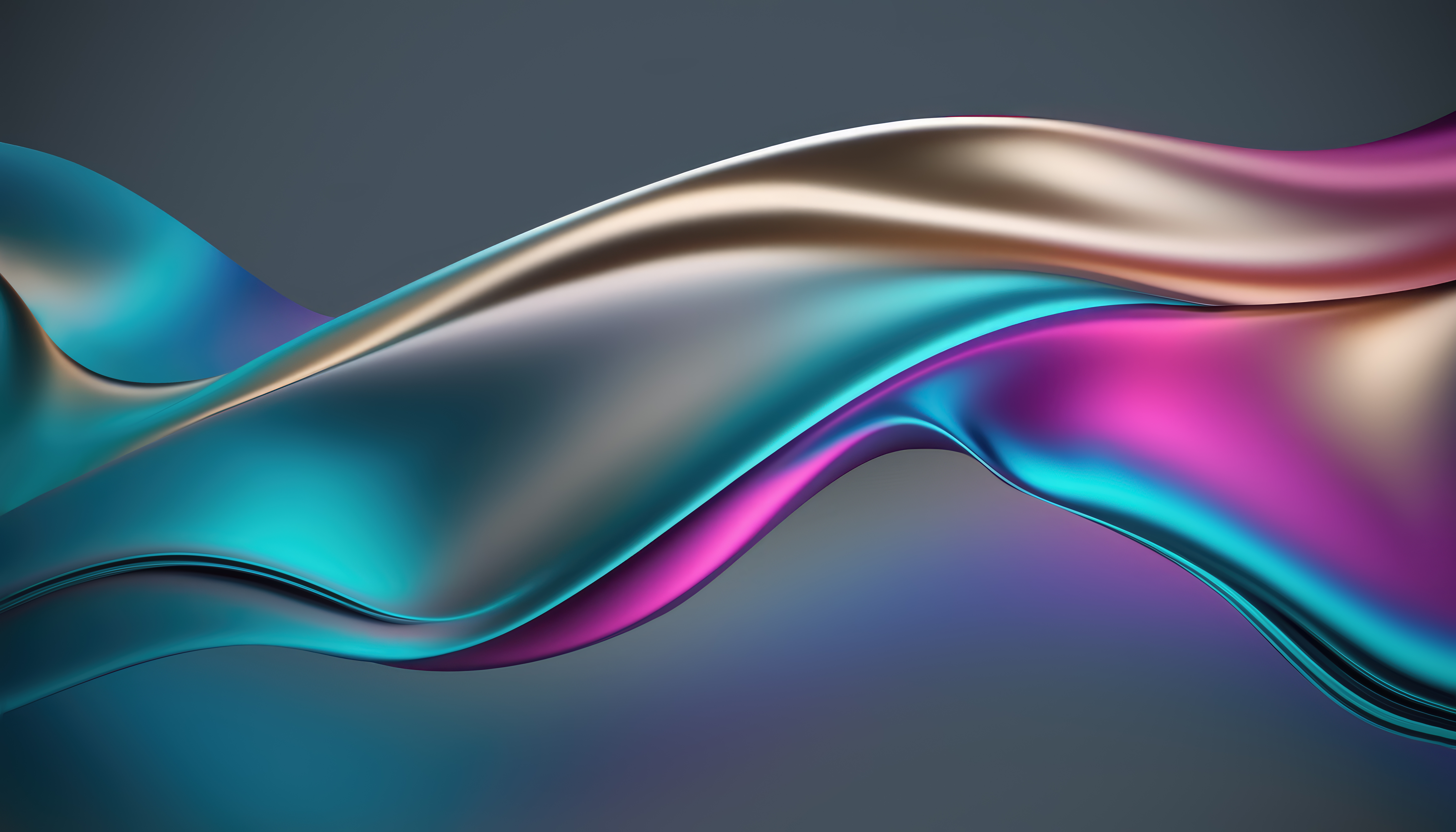
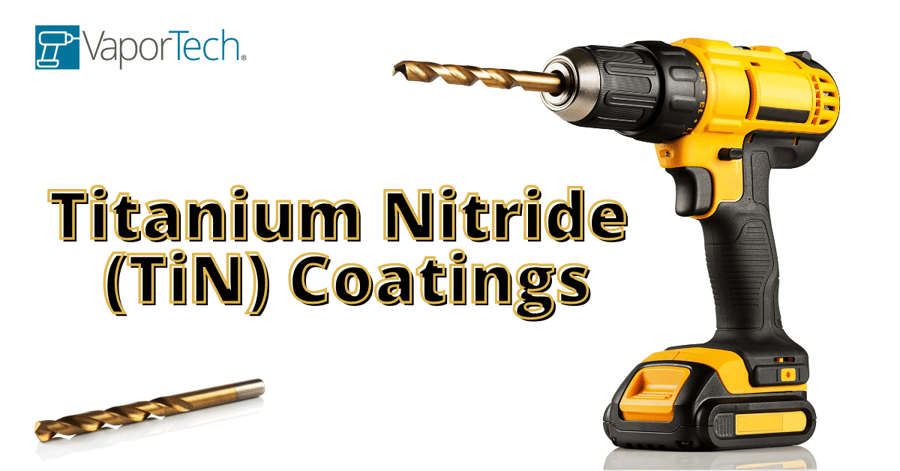
What Is Titanium Nitride Coating—and What Are TiN Coatings Used For?

No Ph.D. Required: VaporTech Machines Make The PVD Coating Process Easy
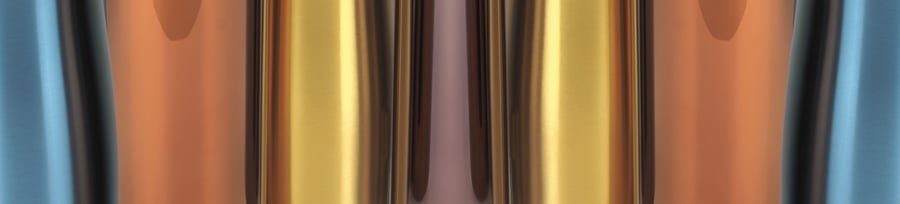