What Is Titanium Nitride Coating—and What Are TiN Coatings Used For?


- Titanium nitride (TiN) coating: TiN coatings provide high hardness, thermal stability, and oxidation resistance for industries including biomedical, automotive, and tooling.
- PVD deposition techniques: TiN coatings are applied using magnetron sputtering or cathodic arc evaporation
- TiN coating properties: TiN's properties include biocompatibility, increased gloss, reduced friction, and expanded substrate compatibility.
Titanium Nitride (TiN) coating is one of the most well-known choices for physical vapor deposition (PVD) and has been a mainstay of product finishing for decades. Customers like TiN because of its good mechanical properties and lustrous gold color. The combination of a non-metallic element (Nitrogen) with a transition metal element (Titanium) forms a refractory (resistant to alteration) material. The material exhibits many attributes associated with refractory nitride materials. These attributes include:
- High hardness
- Good electrical and thermal conductivity
- Chemical stability
- Thermal stability
- Oxidation resistance at elevated temperatures.
Purposes of TiN Coating
TiN has excellent mechanical, corrosive, and thermal properties to fit a range of applications. Manufacturers use TiN coatings in several industries, including biomedical, automotive, tools and tooling, and outdoor sports. The TiN cubic structure is very compatible with most metallic substrates, ensuring good coating adhesion on many substrates.
Did you know?
One of TiN’s more unique properties is its compatibility with biological structures, making it suitable for medical implants and devices intended for internal use for biological organisms.
How are TiN coatings deposited?
Depositing TiN using PVD techniques typically involves a solid target made from very pure titanium, argon gas, and nitrogen as the reactive gas. The titanium (Ti) atoms/ions from the target react with the nitrogen (N) atoms from the reactive gas to create TiN. TiN formation requires relatively high activation energy generated by either heat or ion energy. Suppose the process does not contain enough energy during coating deposition. In that case, the resulting phase will only consist of Ti, which is much softer than TiN and exhibits a metallic gray appearance rather than gold.
Have questions about Titanium Nitride Coatings? Contact us today for more information.
Use magnetron sputtering or cathodic arc to apply TiN coatings
Several PVD methods are used for TiN synthesis. Today, the most common methods are magnetron sputtering or cathodic arc evaporation. Each method has benefits and challenges, and each VaporTech® deposition system can use either technique or both.
The available color range deposited by the cathodic arc is broader than that from magnetron sputtering systems. Magnetron sputtering TiN is typically less yellow and redder than TiN deposited by cathodic arc evaporation. The color changes are caused by differences in ion energy, as discussed below.
Cathodic arc for TiN coatings
Cathodic arc evaporation generates many ions that cause enough energy to produce TiN without substrate heaters. You can run the process at low enough temperatures to coat substrates with melting temperatures as low as plastic. Vapor Technologies customers can deposit cathodic arc TiN coatings in our VTi™-series machines. Below is a cross-sectional SEM micrograph of a TiN film deposited in our VT-1500i™ system.
One intrinsic disadvantage of cathodic arc processes is the formation of macroparticles. These particles can produce hazier films with higher coefficients of friction. However, at VaporTech, we developed a process that deposits TiN films (and others) with significantly fewer macroparticles. The results show an increase in gloss of more than 20%. This process improves the look of the coating and improves its wear and coefficient of friction.

Surface SEM images of TiN films deposited in the VT-1000i™ system with the original process (left) and the improved (right).
Ideal PVD Systems for depositing TiN coating
The new V.MAX1500 PVD coating system for industrial products creates TiN coatings for consistent coatings that enhance your product's functionality. Check out this multisource, flexible machine for your functional coating needs.
About VaporTech
Headquartered just outside Boulder, Colorado, VaporTech produces cathodic arc, magnetron sputtering, and combination (hybrid) systems in a range of sizes. The company helps customers optimize surface finishes, including TiN coating, for their specific applications. For more information, contact us today at vtsales@vaportech.com
Recent posts
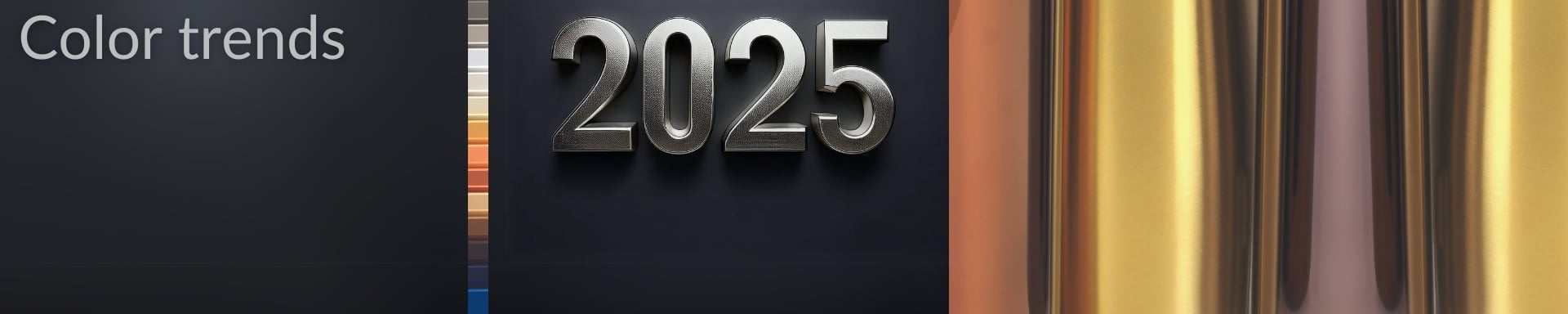
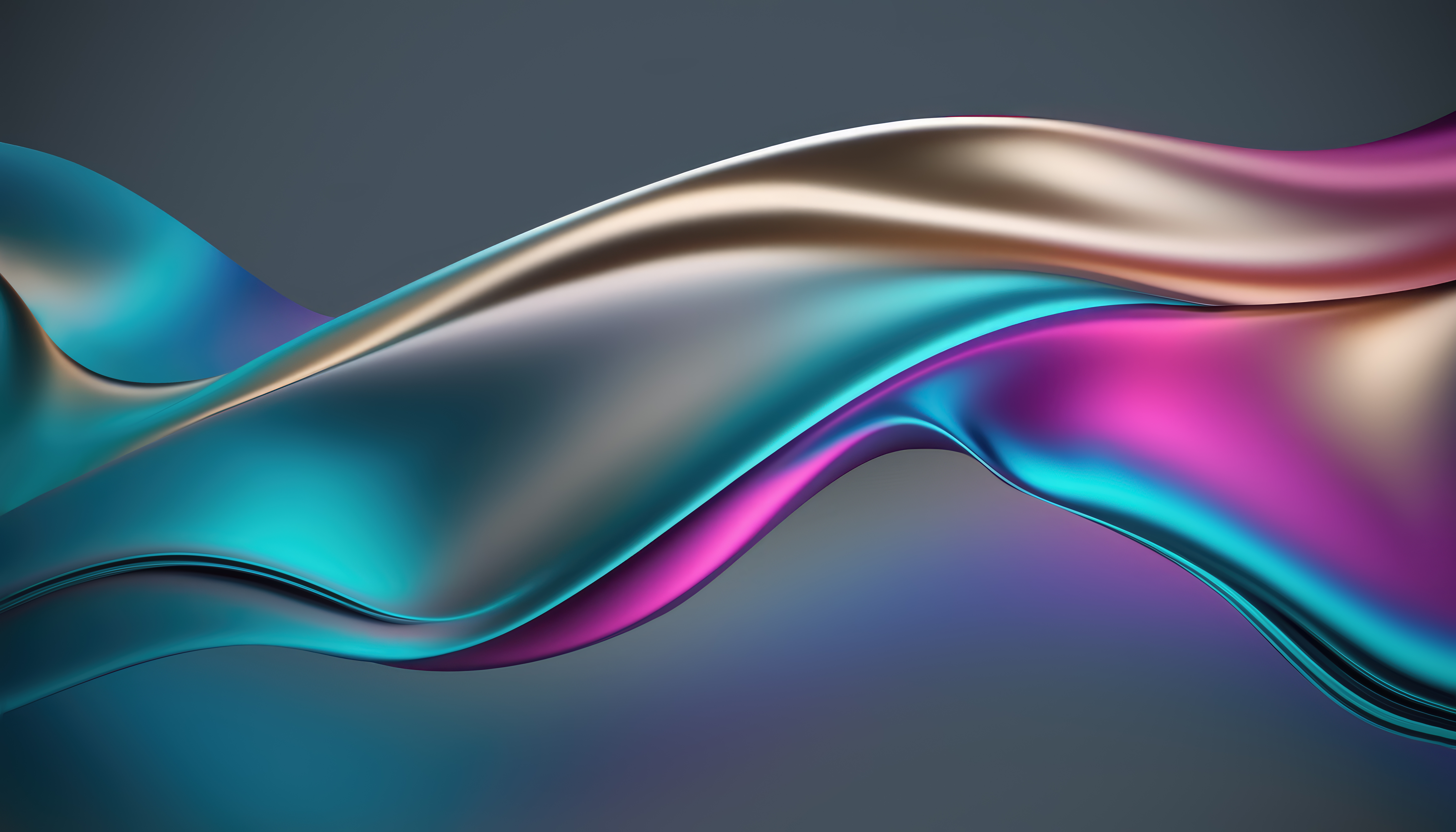
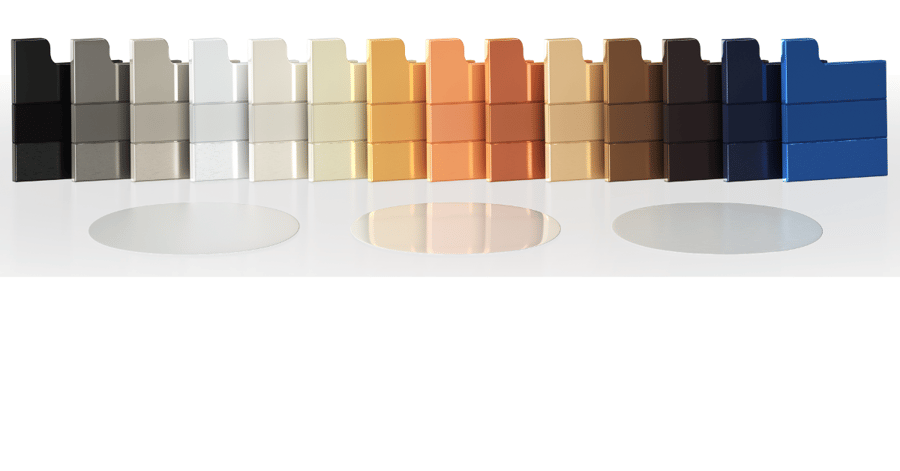
Use Our Zirconium Coating Technologies for Outstanding Durable & Decorative Coatings
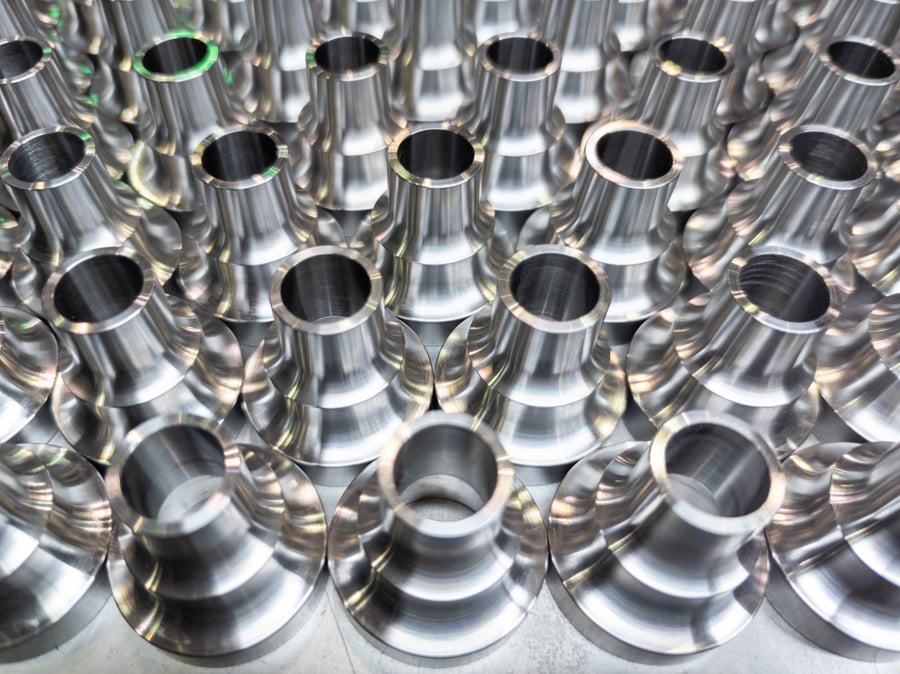
A Brief Introduction to Tribological PVD Coatings
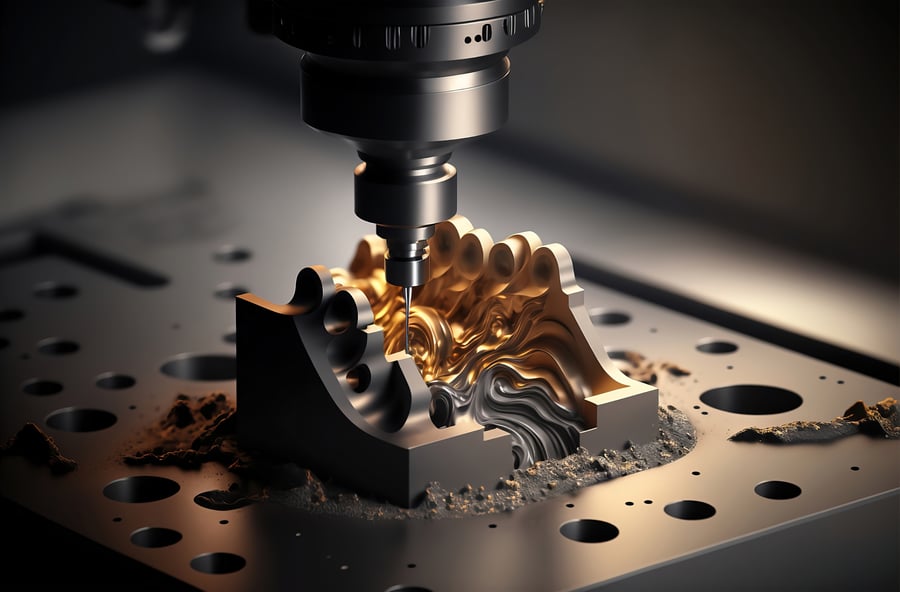