Preparing Your Facility for a Vapor Deposition Coating System


This post covers general information about preparing a facility for a physical vapor deposition (PVD) coating machine. If you purchase VaporTech® thin-film deposition equipment, we provide a detailed site preparation checklist, offer purchasing assistance if needed, and help you create an efficient, organized schedule to make the process as smooth as possible. Contact us for further information.
Congratulations on choosing a PVD coating system for your thin-film coating application. Thin-film equipment manufacturing companies typically take at least a few months to build and deliver a PVD coating system. While you’re waiting to start using thin-film deposition technology, you can complete your facility preparation activities. Following the steps below, you can prepare for your PVD & DLC system, a successful installation, and a fast production scale-up.
Facility requirements for a PVD coating system
Environment
A PVD system operates in your existing manufacturing facility. If it’s comfortable for your employees, it’s typically suitable for the system. It is best practice to protect the system from particulates from grinding or other metal fabrication operations. Therefore, position your PVD system away from this type of machinery. To keep the system separate, add room dividers or improve air handling systems for a relatively dust-free environment that keeps parts clean. PVD coaters provide better coating consistency and higher yields with these precautions.
Although PVD machines operate successfully in humid environments worldwide, they are vacuum systems that remove air and water vapor from the chamber when running a process. A lower-humidity facility means a faster pump-down time and saves several minutes in your PVD cycle time.
The size and space vary depending on machine size and configuration. We often tell customers to imagine the size of a home garage. A small system requires approximately one garage space, while a large system requires a two-car garage floor space. Remember that in addition to the PVD system, you may need additional space for ancillary equipment (more on that later).
Utilities
Your PVD system includes vacuum pumps, power supplies, heaters, and other electrical systems. Each component uses energy during various parts of the coating cycle. Here’s a quick overview of utility and related equipment requirements.
Electrical
PVD systems operate on 480-volt, 60hz, 3-phase power (380-400V, 50hz is also available). The current draw depends on the model and configuration but typically ranges from 160 to 270 amps.
Network/internet access: We recommend internet access as our systems ship with a secure internet gateway for remote monitoring and troubleshooting.
Cooling water
The PVD system requires cooling water from a standalone or facility water chiller. Cooling water keeps the PVD machine operating at its optimal temperature. It enables a lower-temperature cathodic arc deposition process that coats items such as plated plastics or zinc die-cast parts.
Process gases
The PVD cycle uses process gases in trace amounts to create various coatings. Argon, nitrogen, oxygen, methane, or acetylene are gases common in PVD coating and come in bottles like those used in welding operations. For example, to create titanium nitride (TiN) coatings, we start with a solid titanium source and combine it with nitrogen gas. Our systems' specific coating “recipe” automatically meters gases as needed during that cycle.
Compressed air
The system requires a small amount (0.85 m3/h) of clean, dry compressed air to operate various pneumatic valves.
Ancillary equipment
Now that we’ve covered basic PVD thin-film deposition system requirements, let’s move on to ancillary equipment. VaporTech has relationships with many suppliers and can assist with purchasing these items. This list includes:
Additional Items
- Helium leak detector for vacuum diagnostics
- Industrial vacuum for chamber cleaning
Cleaning and handling parts before PVD coating
Cleaning
Clean parts are essential for a high-quality coating operation. Manufacturers can use automated or manual aqueous or non-aqueous cleaning options based on the expected types of contamination (oils, particulates, etc.), substrate material, part geometries, and production quantities. In addition, a grit-blasting cabinet can help clean racks, internal chamber shields, and other machine components during maintenance.
Parts handling
Store, load, and unload parts on parts racks. These stainless-steel racks come in various shapes and designs for different part sizes and geometries. Racks are typically stored and transported on rack carts. Wheeled carts are an easy, efficient way to transport and store part racks. We recommend creating a parts staging area to store parts in a clean, dust-free environment.
Your facility is ready! It’s time for PVD equipment delivery.
When you’re ready to bring in your thin-film deposition machine, you must prepare to receive and install it. Most VaporTech PVD coating machines come completely assembled on a single skid. All that’s needed is a forklift for unloading and basic rigging equipment to move the equipment in place.
Unless you’re confident moving large equipment, we recommend hiring a professional rigging company to complete this process for you. VaporTech staff will assist with on-site equipment startup and provide your team with detailed operation and maintenance training.
More information about vapor deposition from VaporTech
Here are some additional resources for PVD coating information:
Please email us for detailed information about our systems and the coatings they produce!
Recent posts
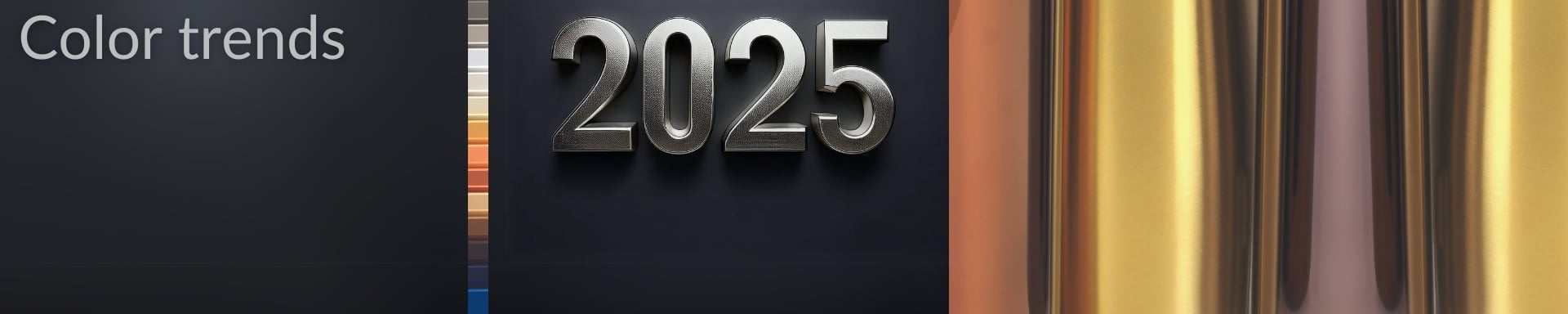
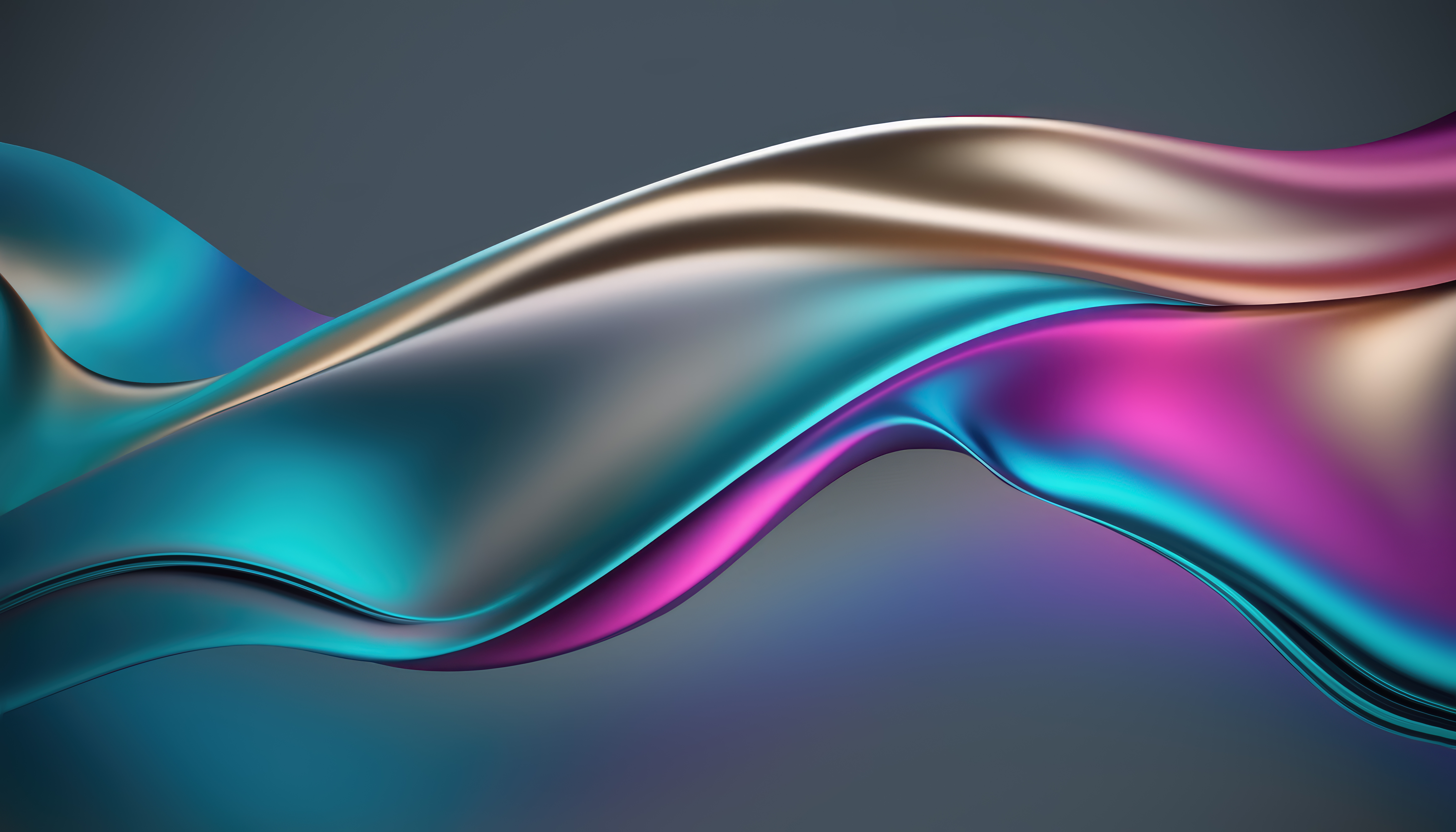
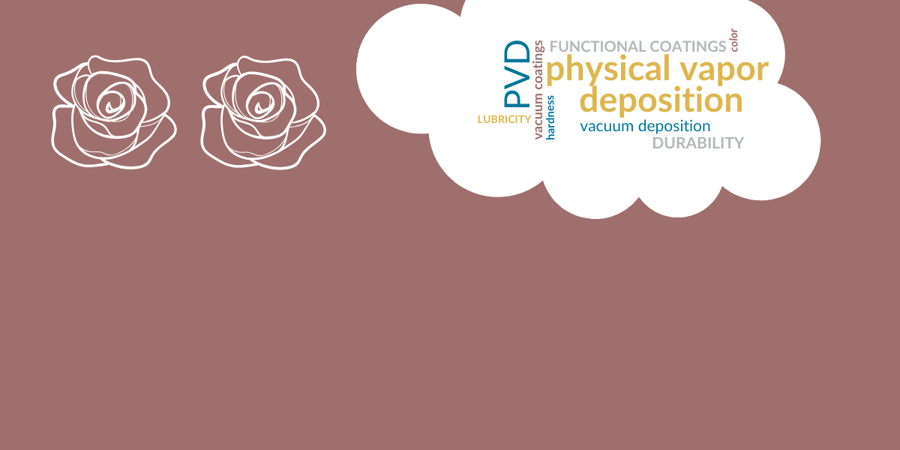
Why Is Physical Vapor Deposition (PVD) Also Called ‘Vacuum Coating’ Or ‘Vacuum Deposition?’
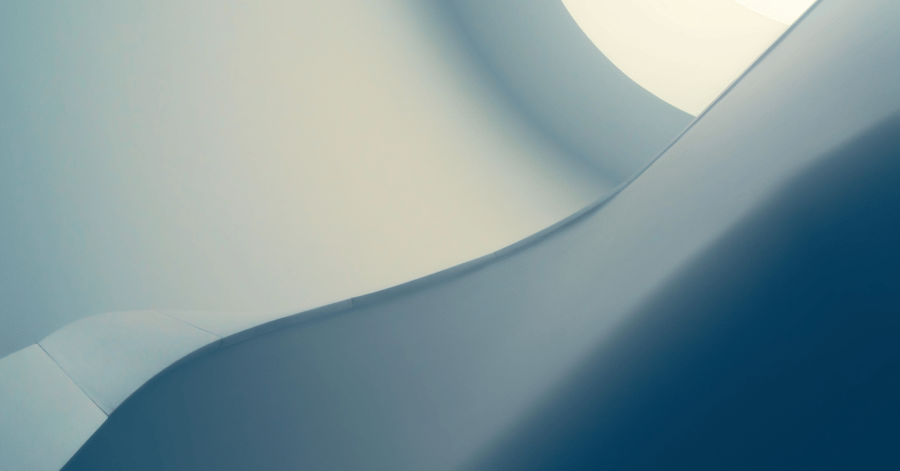
What is PECVD? Use it to Create DLC coatings in Your Vapor Deposition System.
