Durable PVD Finishes & Color Coatings: The Future Is Bright


Wondering how PVD color coatings are made and what colors you can get? Read on.
To create color PVD finishes, you deposit films with specific stoichiometries (ratio of certain elements). Typically, you take a base metal and react it with a reactive gas to form a very thin ceramic compound. For example, titanium coatings are usually silver or gray when deposited, but adding nitrogen to form a titanium nitride (TiN) compound produces a dazzling gold color. Furthermore, you can create riveting rose gold colors if you add a small amount of carbon to TiN to form titanium carbonitride (TiCN). The table below displays some element combinations required to create specific PVD coating colors.
You’ll notice that certain base metals can produce many different PVD finishes and color coating combinations, from gray to dark bronze to blue. In contrast, others are limited to only gray-toned colors. This difference is why most durable decorative films are titanium- or zirconium-based. Another reason is that the compounds that create the most striking colors exhibit excellent wear- and chemical-resistant properties.
Users deposit various PVD coating colors on many different textures with these durable color coatings. Since all color PVD finishes match the surface texture of your substrate, each distinct surface creates a specialized look and feel. Depositing on a glossy substrate makes the coating appear vibrant, while depositing on a textured substrate provides a more muted look.
Some PVD coatings generate the same color regardless of film thickness (i.e., TiCN), and some are thickness-dependent (most oxides). To provide a uniform color throughout a 3-dimensional part, colors that require specific coating thicknesses (also known as interference films) may require specialized racking.
Contact us today if you are looking for more information about racking and color uniformity.
How long do durable color PVD coatings last?
Decorative thin-film coatings are durable: they provide excellent wear and corrosion resistance. However, they don’t have the same tribological attributes as the thicker films designed for wear applications. Since the primary coating function is to create cosmetic finishes, not tribological, the thickness for most decorative films is less than 0.5 µm.
Durable Color Coatings
All our durable color PVD coatings can withstand abrasion against steel wool. The image on the left shows a ~0.4 – 0.5 µm thick ZrN coated panel subjected to our “steel wool scrub test” for 3000 cycles. This test involves attaching a 3.8 lbs. weight to a coarse steel wool pad that is cycled against the coated panel. As you can see, the steel wool did not damage the panel. Further chemical elemental analysis of the coating depth profile conducted with our Glow Optical Discharge Spectrometer (below) shows that most of the coating remains and may withstand many more cycles!
Are PVD color finishes a good fit for your application?
All VaporTech durable-decorative coatings are deposited with our LTAVD® (Low-Temperature Arc Vapor Deposition) cathodic arc technology. This process produces coatings that would be very difficult for other PVD technologies to create at much lower temperatures while still maintaining high deposition rates with great properties. Therefore, we can apply these coatings to various substrates (including plastic and zinc).
What coating color combinations can VaporTech create?
VaporTech offers 20 standard colors and creates custom coatings for use in our systems to match the exact decorative finish required. Standard colors include:
- Black
- Cool Graphite
- Graphite
- Chrome
- Stainless Steel
- Nickel
- Gold
- Rose Gold
- Dark Copper
- Light Bronze
- Bronze
- Dark Bronze
- Blue Black
- Vivid Blue
- Rainbow
- Purple
Because PVD coatings have such excellent wear resistance while providing a high-value appearance, you have many suitable applications. We provide coatings for plumbing products, exterior and interior door hardware, lighting, jewelry, sporting goods, automotive products, and more.
Recent posts
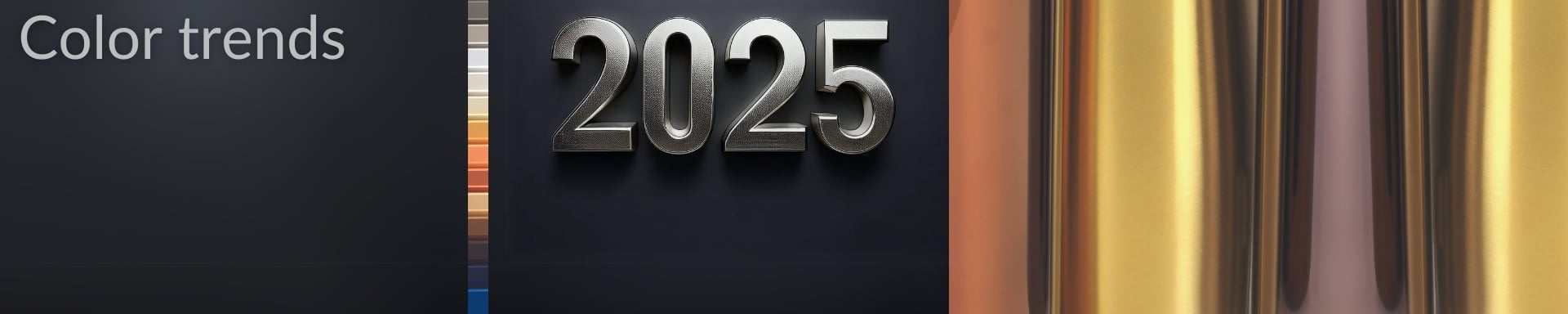
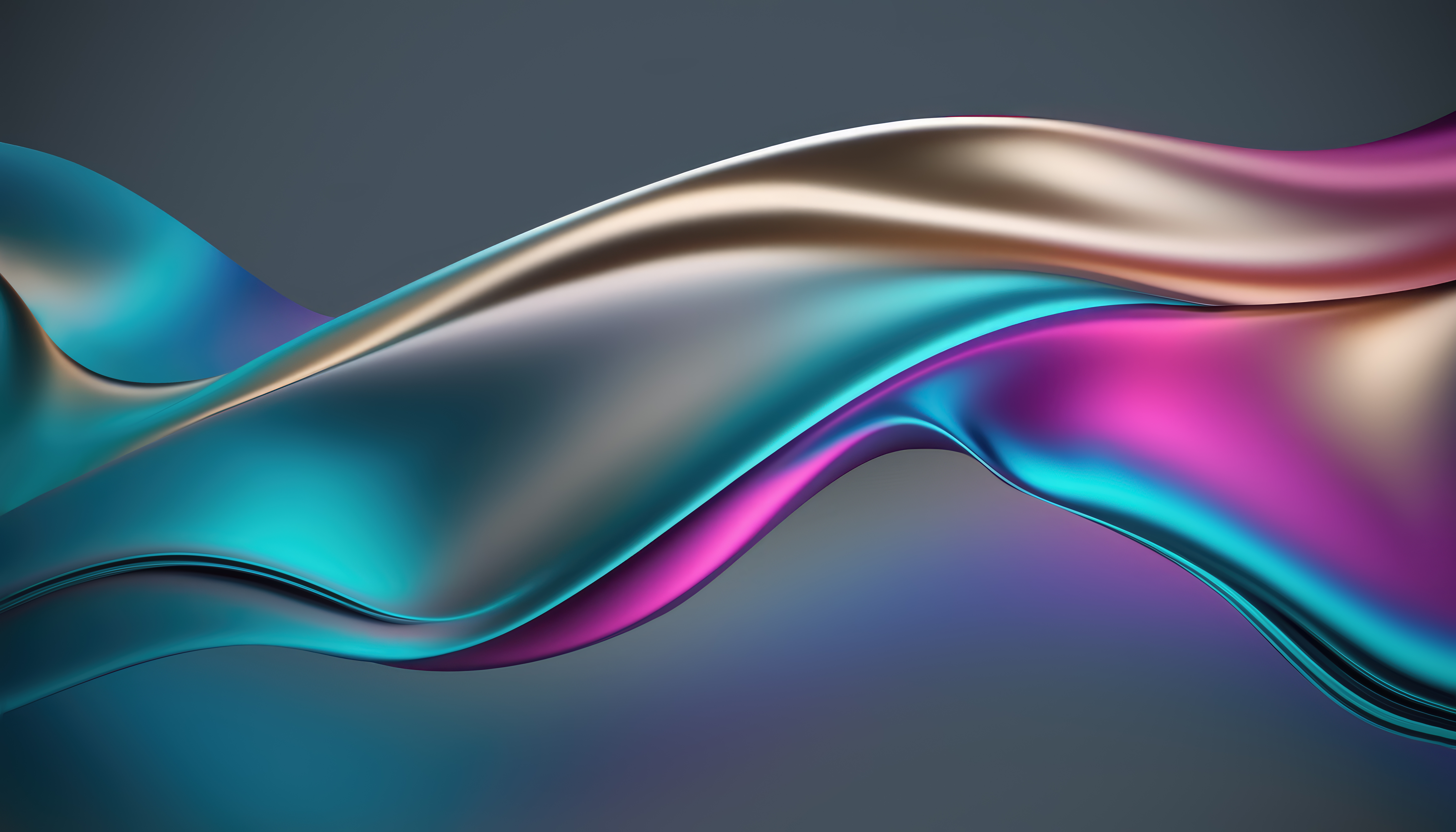

Color PVD Coatings: The Future Is Bright
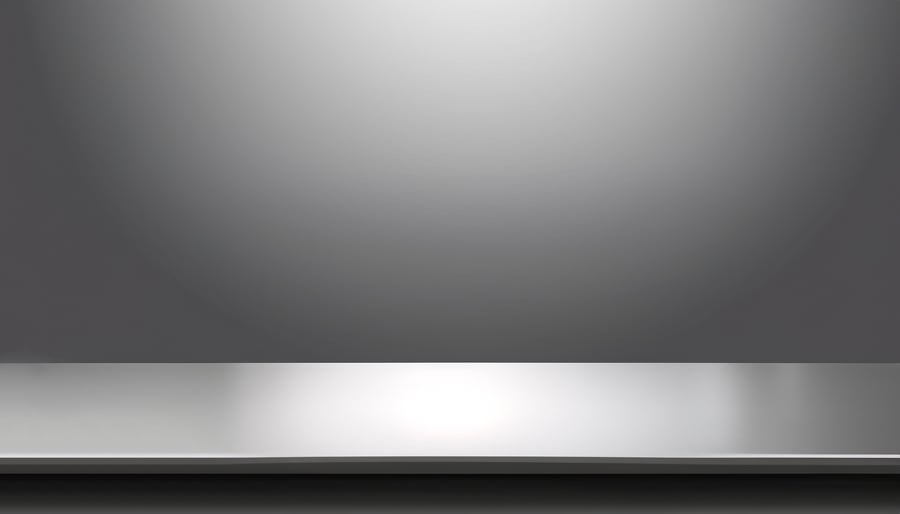
How to Clean Parts Before PVD Coating
