PVD Machine Vacuum Pumps & Vacuum Pumping Technologies


Physical vapor deposition (PVD) and plasma-enhanced chemical deposition (PECVD) processes are conducted at sub-atmospheric pressures. Therefore, generating and maintaining a vacuum environment is essential to designing and specifying the equipment for these processes.
Most industrial vacuum deposition chambers are manufactured from stainless steel and have access ports and doors sealed with elastomers. Once parts to be coated are placed inside the chamber, the system is pumped down to a base pressure that varies depending on the degree of residual air compatible with the process and the desired purity of the coating material. That base pressure can vary from ultra-high vacuum in the 10-8Torr[1] range or lower for some semiconductor applications to a few Torr in thermochemical processes such as plasma nitriding. Base pressures between 1x10-6 and 1x10-4Torr are typical for most PVD and PECVD industrial applications.
The PVD process and the PECVD process
PVD and PECVD processes occur at pressures higher than the base pressure as gases are introduced in the chamber at set flows, and the pressure is controlled to the desired process conditions. Vacuum pumps are used to achieve the pressure levels required for PVD and PECVD.
It may surprise some that many different types of vacuum pumps are based on operating principles and achievable vacuum levels.
Gas transfer and gas-binding pumps used in vacuum coating
Pumps can be divided by operating principle into two main groups: gas transfer, meaning that gases are moved through the pump and exhausted to the atmosphere, and Gas-binding pumps, in which gases are trapped. Special precautions are taken when hazardous gases are used, such as scrubber systems that treat the exhaust gases before their release into the atmosphere. All PECVD equipment and most PVD process systems use some type of gas-transfer pump.
For vacuum levels at or below 1x10-3 Torr, more than one type of pump is required. That’s because the nature of the interaction between gas molecules changes as pressure falls, affecting how the gas flows – from a viscous flow at low vacuum through a transition regime (Knudsen flow), to molecular flow at high vacuum.
Types of vacuum pumps used in PVD coating equipment
During the initial pump down from atmospheric pressure (roughing), the most common pumps used in the industry are rotary vane pumps, screw pumps, and roots pumps. These pumps generally perform at their best from atmospheric pressure down to the 10-2Torr range; their pumping speeds decrease rapidly below those pressures. Rotary vane and screw type pumps are often used in tandem with roots pumps as the latter outperforms both other pumps at pressures below the 1 Torr range – this arrangement is sometimes referred to as mechanical pump stack.
A different pump is needed when a higher vacuum is required, either for base pressure or suitable process conditions. These high-vacuum pumps can operate in the molecular flow regime but cannot pump in the range where roughing takes place. Therefore, during pump down, there is a hand-off to the high-vacuum pump at a given crossover pressure, typically in the 5x10-2 to 10x10-2 Torr range.
Diffusion and turbomolecular pumps are the most common high-vacuum pumps in industrial applications; see Figures 1 and 2. Both are classified as kinetic vacuum pumps, a branch of the gas transfer classification. For these pumps, gases pass through but aren’t compressed enough to be exhausted to the atmosphere, so another pump is connected to their outlet to perform that task.
Figures 1 & 2: diffusion pump, above. Turbomolecular pump, below.
In some cases, the pumps employed during roughing switch to pumping the outlet of the high-vacuum pump after crossover. That part of the pumping system is called the "foreline,” and the pump performing that function is called the “backing pump.”
A simplified example of a high vacuum system containing pumps and valves is shown in Figure 3.
Figure 3. Schematic representation of vacuum system with chamber, pumps, and valves.
The PVD machine vacuum pumping sequence
A typical pumping sequence starting with the chamber at atmospheric pressure is listed below and shown in Figure 4.
Step 0: The chamber is at atmospheric pressure and sealed. The gate and roughing valves are closed, and the foreline valve is open. Note that when kinetic high vacuum pumps such as the turbomolecular and diffusion pumps are running, a low pressure must always be maintained on their exhaust.
Step 1: During rough pumping, the foreline valve is closed, and the roughing valve is open.
Step 2: At the crossover pressure, the roughing valve is closed, the foreline valve is opened, and the gate valve is opened.
Figure 4. The sequence of valve actuation during pump down of the system.
PVD and PECVD processes occur with gases flowing through the high vacuum pump or directly through the mechanical pump stack, depending on the volume of gas and pressure used during the process. Process pressure in the chamber can be controlled upstream, i.e., by actively controlling the amount of gas introduced in the chamber or downstream, by actively changing the conductance to the pump. Downstream control is achieved by installing a throttling valve in front of the pump.
Vapor Technologies, Inc. (VaporTech®) employs high vacuum pumps and mechanical pump stacks in vapor deposition systems.
Glossary of PVD system vacuum pumping terms
Vacuum: state of gas in which the density of molecules is lower than that of a gas at the local atmospheric pressure.
Base pressure: lowest pressure (highest vacuum) achieved in a vacuum chamber before the start of a process.
Roughing: In vacuum jargon, roughing means the initial pump down from atmosphere.
Foreline: section of pumping line between the exhaust of a high vacuum pump and a pump that can operate at higher pressures (the backing pump).
[1] 1x10-8 Torr = 0.00000001Torr. For reference, the atmospheric pressure at sea level is 760Torr.
Recent posts
Lorem ipsum dolor sit amet consectetur.
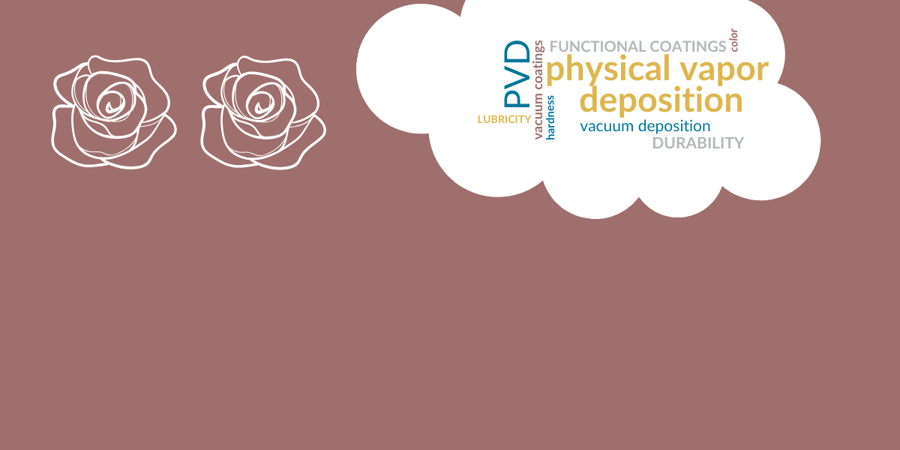
Why Is Physical Vapor Deposition (PVD) Also Called ‘Vacuum Coating’ Or ‘Vacuum Deposition?’
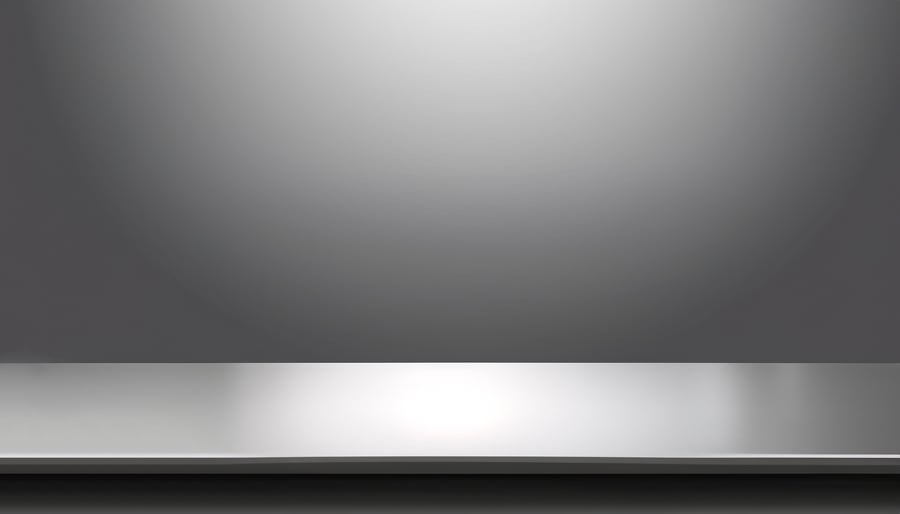
How to Clean Parts Before PVD Coating
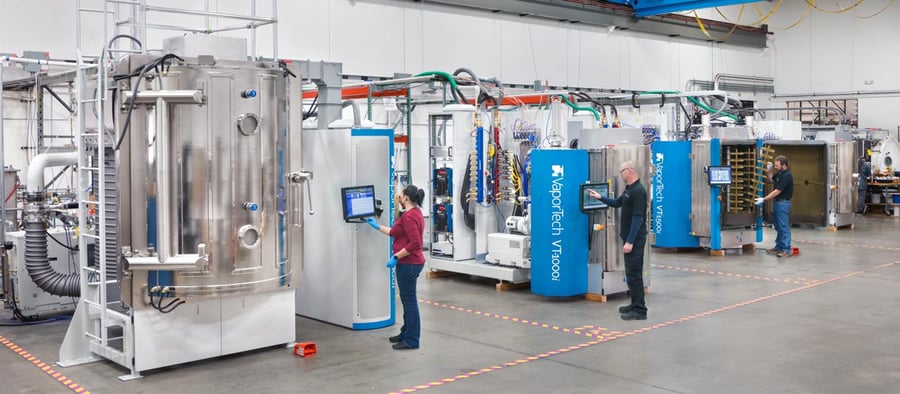