Are Any Everyday Products Thin-Film-Coated? Common PVD Applications Include Faucets, Auto Parts, Tools


Q: What do your car’s trim, common tools, and the kitchen faucet you just bought for a home improvement project have in common?
A: They probably went through a thin-film deposition process in a vacuum system.
Thin-film deposition technologies, like physical vapor deposition (PVD) or chemical vapor deposition (CVD), are most commonly known for their use in producing microelectronics and sensors. We are far less familiar with applying these technologies for more common everyday products, though manufacturers have been using them since as far back as the 1930s.
Everyday common thin-film applications
Several good reasons exist for the widespread application of vacuum thin-film deposition beyond microelectronics. PVD and CVD processes in a vacuum chamber provide unmatched control over material properties like composition, hardness, conductivity, transparency, or color, to name a few. This control enables manufacturers to engineer thin films with properties tailored to their application and product.
Here are a few examples of thin-film technology applications on everyday products:
Home hardware – PVD-coated products like faucets, kitchen & bath, and door/window hardware
Home hardware thin-film applications: If your faucet looks like stainless steel, nickel, bronze, black, or a shade of gold, it is most likely coated with a PVD film for color and durability. For long-lasting performance, your faucet may also include internal water metering valves coated with a PVD diamond-like carbon layer (DLC) film.
Automotive thin-film applications
Automotive PVD applications: PVD equipment and coatings improve the function and durability of high-performance engine components, creating an upscale look for auto and motorcycle interiors and trim. PVD is a cleaner alternative to hexavalent chrome for this purpose.
With PVD coatings, your critical components last longer, operate more efficiently due to lower friction, withstand high temperatures, and resist corrosion.
The trim in your car (or private jet, if you happen to own one) may have gone through a PVD process to apply that stunning metal or dark DLC finish onto the metal or plastic parts.
Your car’s headlamps are a piece of molded plastic. A thin PVD layer of aluminum acts as a mirror to reflect the light from the bulb or LED.
PVD-coated drill bits: a bright thin-film application
You will find gold-colored drill bits and other cutting tools in home-improvement stores. These items are not made of gold or painted. Instead, a thin-film application of titanium nitride (TiN) PVD coating is much harder than the drill bit’s steel, so it stays sharp longer.
Jewelry – a durable color PVD use
Jewelry made from precious metals is relatively limited when it comes to color choices. Fashion designers, as well as consumers, like more variety. A common PVD use is applying a durable-decorative metallic finish to jewelry.
Home windows - PVD coated hardware
Your durable window hardware may have a PVD coating (see more information in “home hardware” above).
Those low emissivity (Low-E) windows that keep your home’s energy bill down are likely coated with a thin stack of PVD films to repel heat (infrared) while still being transparent to visible light.
Have a question about PVD coating applications? Contact us to learn more!
How PVD coating works: common everyday thin-film applications
The PVD process used for common thin-film applications vaporizes a solid material in a vacuum. The vaporized material forms a film on a substrate or product. Because deposition happens in a vacuum chamber, the vaporized material remains very clean. With the controlled addition of one or more reactive gases, the vaporized material can be modified in its composition. For example, by adding nitrogen to the process, a vaporized metal will react to a metal nitride. There are several different techniques used to vaporize solid materials in a vacuum. The solid material is vaporized using either a heated crucible, an electron beam, ion bombardment from a plasma, or a cathodic arc.
The CVD thin-film coating process introduces one or more gases into the vacuum process chamber, where they react with the product’s surface at high temperatures.
For PECVD (plasma-enhanced chemical vapor deposition), the chemical reaction is not induced by high temperature but with a low-temperature plasma. The gas is activated or cracked in the plasma to create reactive species, forming a film on the substrate/product surface. Common applications include DLC coating.
About VaporTech
Vapor Technologies (VaporTech®) manufactures PVD and PE-CVD thin-film coating machines—including the new hybrid VT-1500i™ system—for both everyday and specialized thin-film applications. Our patented PVD processes give you high-quality finishes to enhance your common and specialty product applications. Want more information about thin-film applications? Contact us today.
Recent posts
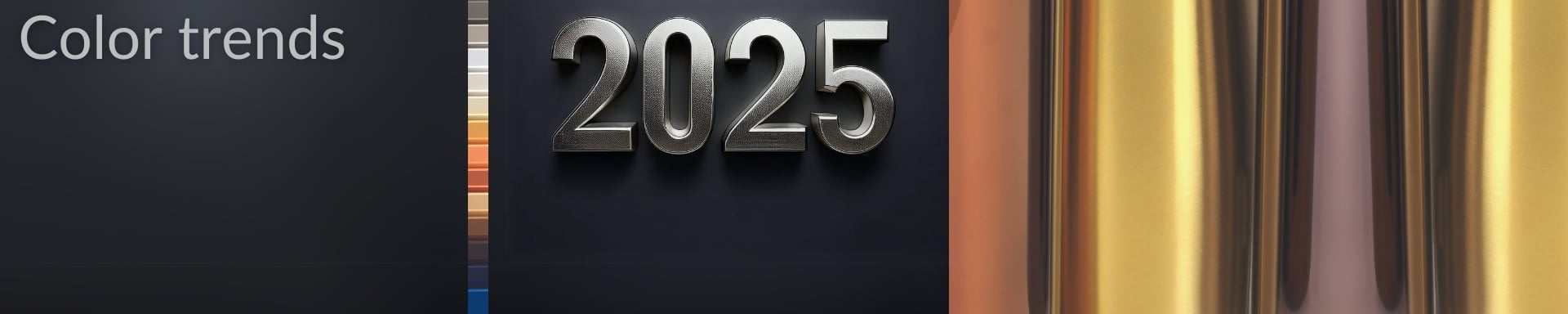
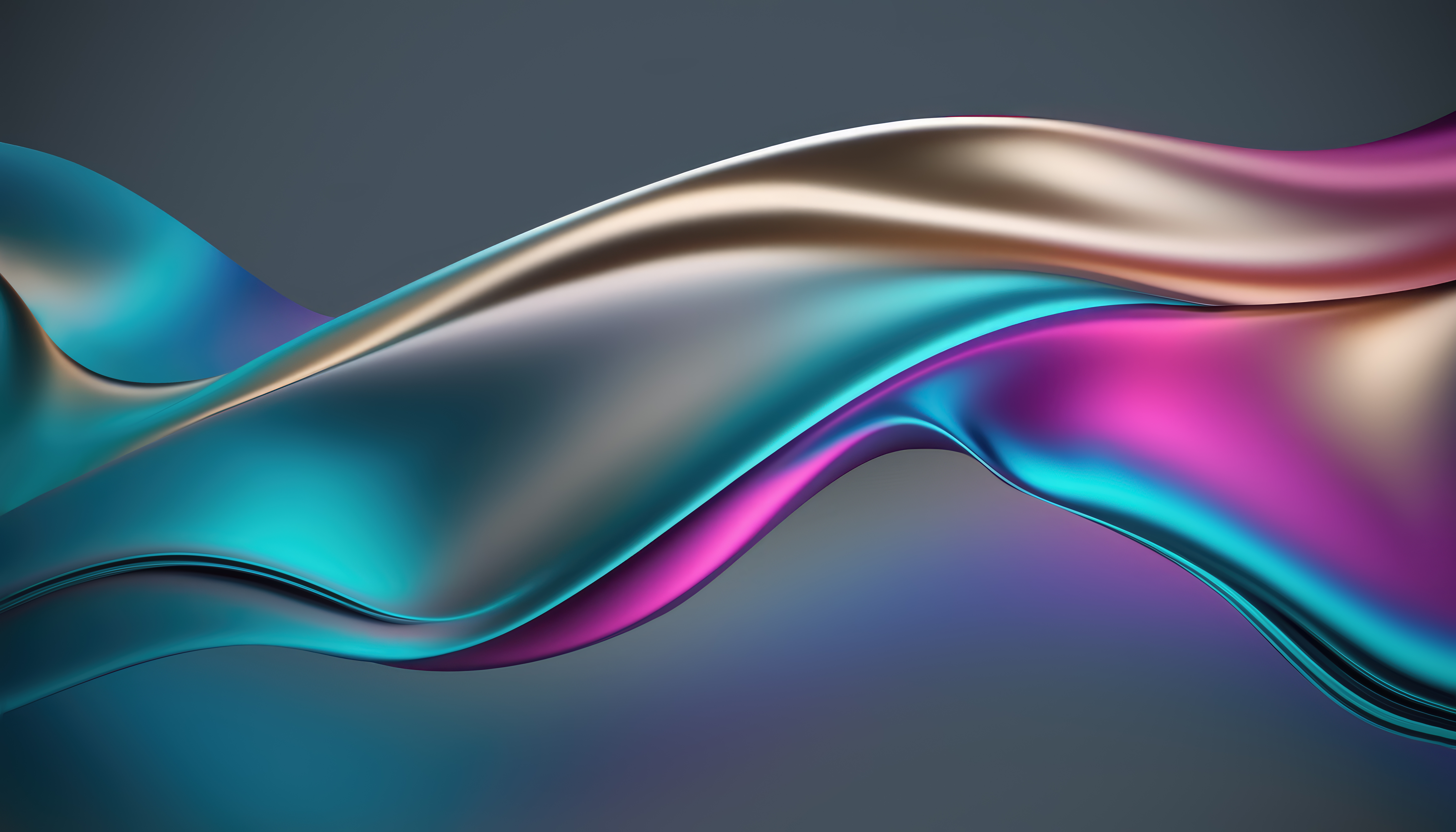
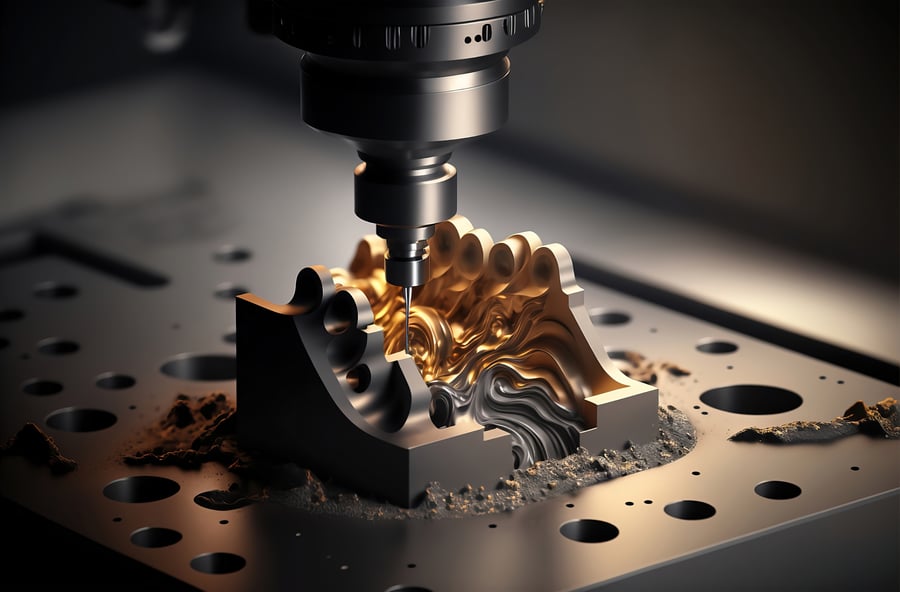
How to Choose the Right PVD Coating for Your Product [webinar, video]
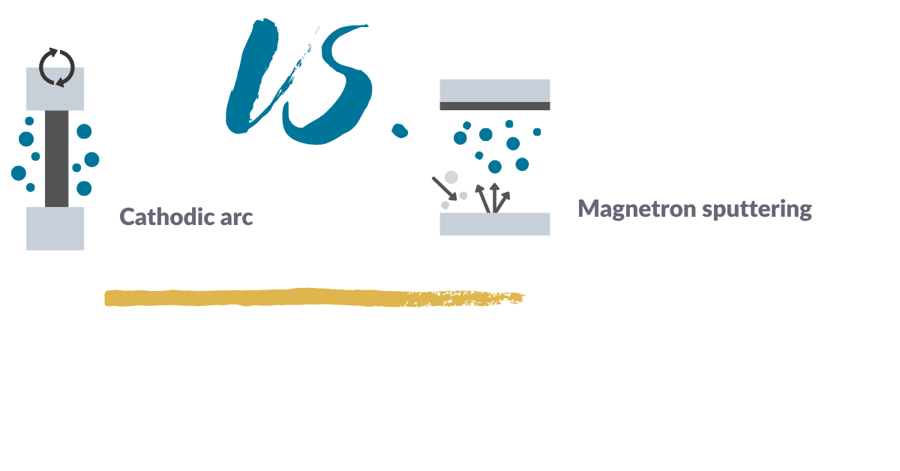
Sputtering vs. Cathodic Arc: Which Physical Vapor Deposition Process Should You Use?
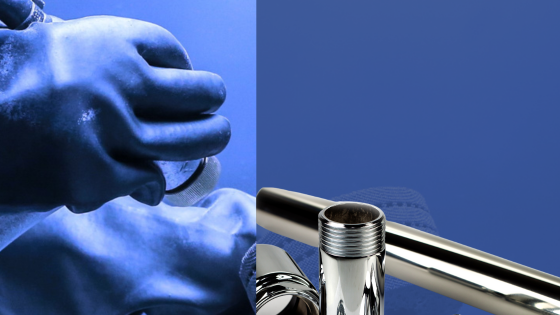