Enhance Implants & Surgical Instruments with PVD Coatings Applied In-House


-
Enhanced implant and instrument performance: PVD coatings improve durability, reduce friction, and enhance corrosion resistance for implants and instruments.
-
Biocompatibility and osseointegration: Titanium and DLC coatings promote cell attachment and minimize ion release for safer implants.
-
Cost-effective in-house solutions: VaporTech® in-house PVD systems lower costs and streamline coating processes.
Metal ion release, wear/friction reduction, osteointegration/cell attachment, and appearance are important characteristics for orthopedic, spinal, and dental implants. Surgical instruments require excellent durability, color coding, reduced light reflection, and, in some cases, low friction. Physical vapor deposition (PVD) coatings deposited by a thin-film coating system prolong your medical product’s life and improve its function by coating its surface with a durable, biocompatible material with distinct metallic colors. With these attributes, PVD-coated implants and surgical devices are safer and longer-lasting, improving patient outcomes.
Common applications
- Surgical Instrumentation
- Orthopedic Implants
- Dental Instrumentation
- Dental Implant Abutments
- Spine Implants
- Extremities
Improve implants & surgical instruments through PVD coating solutions.
- Wear resistance: Coatings such as titanium nitride can enhance the wear and scratch resistance of implants and instruments, reducing the risk of mechanical failure.
- Anti-allergy: PVD coatings can reduce metal ion release by uniformly coating implant surfaces with a metal barrier.
- Corrosion resistance: Certain coatings can protect the implant from corrosion when materials are exposed to bodily fluids.
- Low friction: High-hardness coatings, such as diamond-like carbon (DLC), provide low friction to resist sliding, wear, and corrosion.
- Excellent adhesion: PVD coatings form a strong bond with the implant surface, ensuring long-lasting performance.
- Uniform and precise deposition: PVD allows for precise control over the thickness and composition of the coating, resulting in consistent quality.
- Osseointegration and cell attachment: PVD can be used to uniformly deposit titanium coatings on PEEK or stainless-steel medical devices, improving cell attachment.
Common types of PVD coatings for implants & surgical instruments
Titanium nitride (TiN), titanium (Ti), zirconium nitride (ZrN), and diamond-like carbon (DLC) are a few common coatings for implants and surgical instruments. The choice depends on the components' desired functionality requirements.
- Titanium nitride (TiN) coating: TiN provides excellent wear resistance and can minimize ion release when applied to implants.
- Titanium (Ti): Titanium coatings are commonly used on PEEK or stainless implants to promote cell attachment.
- Zirconium nitride (ZrN): Like TiN coatings, ZrN can improve resistance to wear and corrosion.
- Zirconium-based coatings can also be deposited in a broad range of metallic colors to differentiate surgical tools or other components.
- Diamond-like carbon (DLC): Commonly used on surgical instruments to improve durability, reduce friction, and provide a dark graphite color.
In-house PVD coating for implants & surgical instruments
If you are currently outsourcing coating work, we can help you streamline your supply chain, increase throughput, reduce coating costs, and improve quality. In-house PVD coating offers a low per-part coating cost, often far less than $1 per part.
The new V.MAX1500 PVD industrial products coating system for functional applications creates implant coatings that enhance dental and orthopedic products. Learn more about this multisource cathodic arc/magnetron spotting machine designed for your functional coating needs.
Contact a VaporTech technical sales representative at 303-652-8500 to learn how easy it is to bring PVD coating in-house.Vapor Technologies, Inc. (VaporTech®) designs, builds, and services thin-film deposition systems that deposit PVD and PECVD coatings to improve products worldwide. VaporTech is a subsidiary of Masco Corporation. This year, we're celebrating 30 years as a Masco company. Our sister companies at Masco are industry-leading home product companies, including Delta Faucets and Behr Paint.
Find more information about VaporTech® medical device coatings and in-house medical device coating systems here:
Recent posts
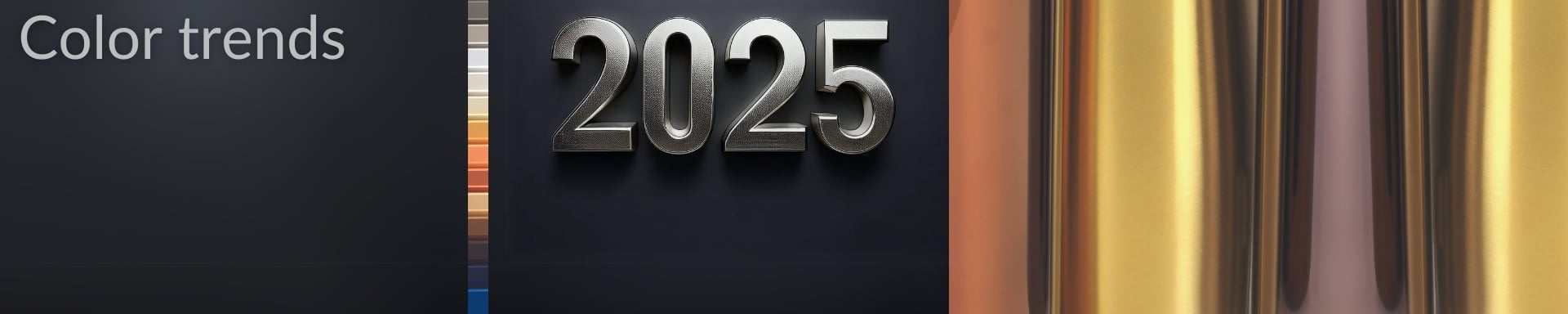
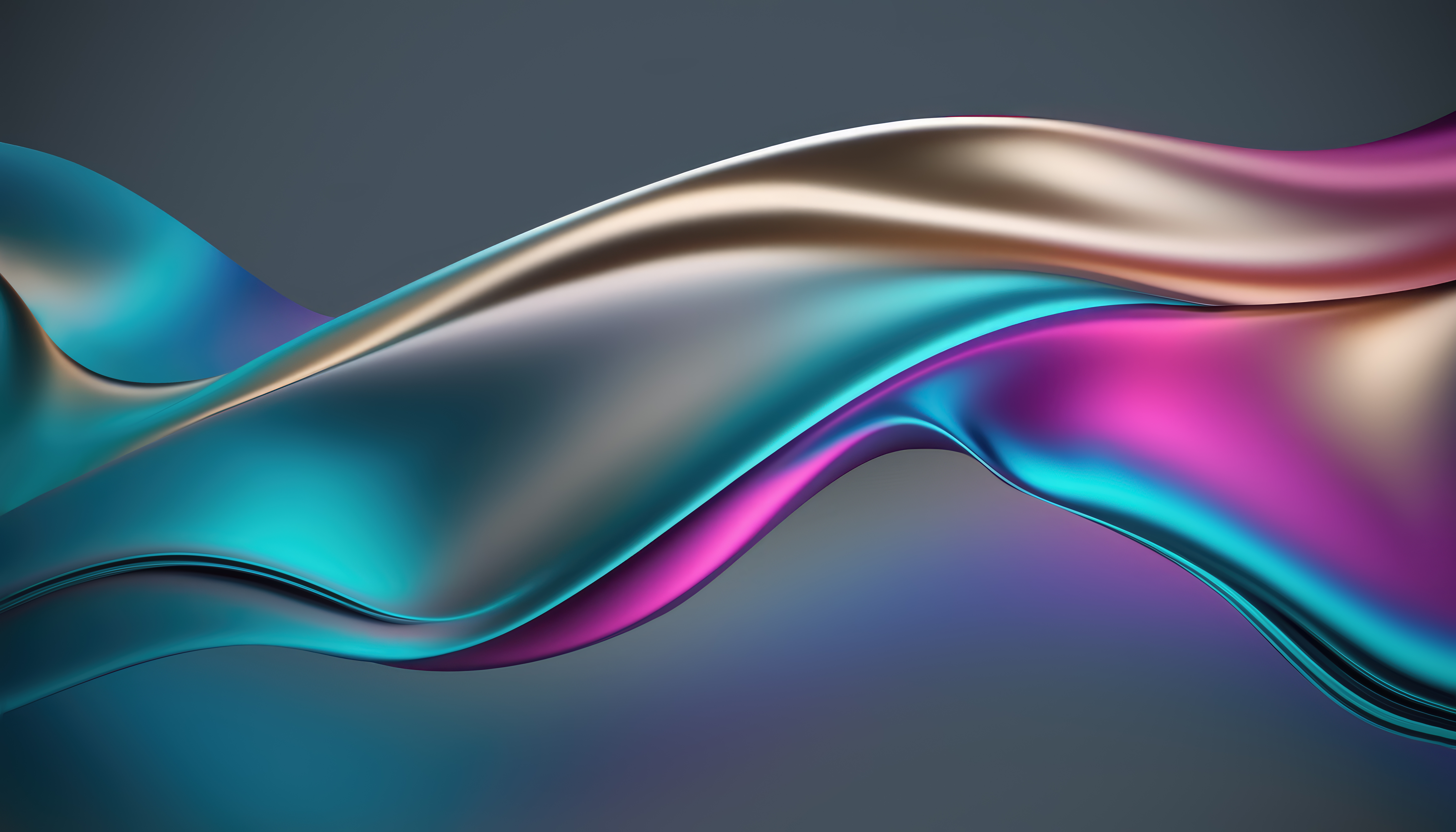
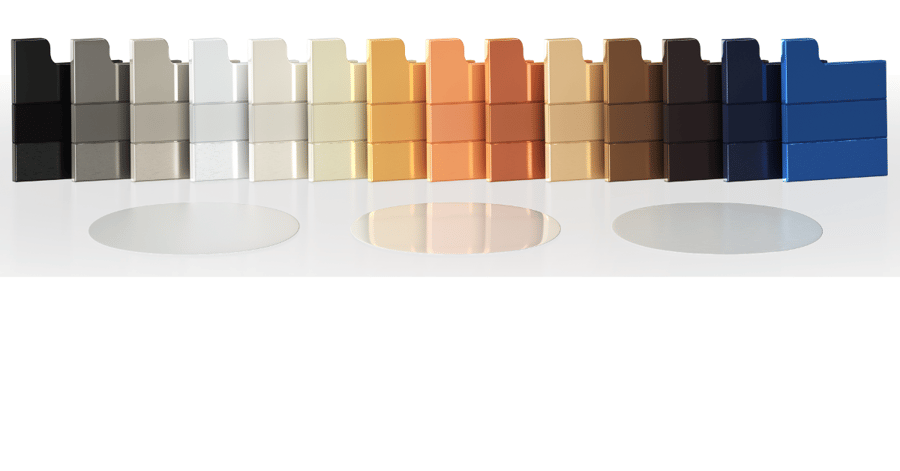
Use Our Zirconium Coating Technologies for Outstanding Durable & Decorative Coatings
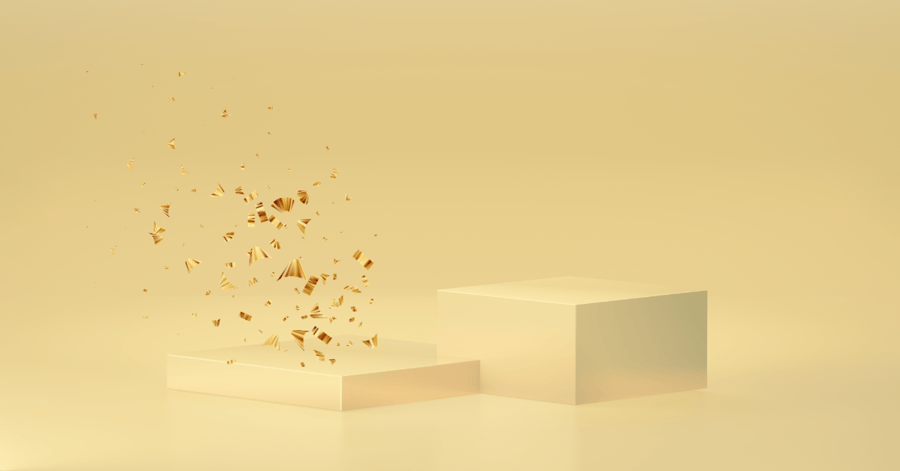
All That Glitters is Not Gold—But It May Be Gold PVD Coating
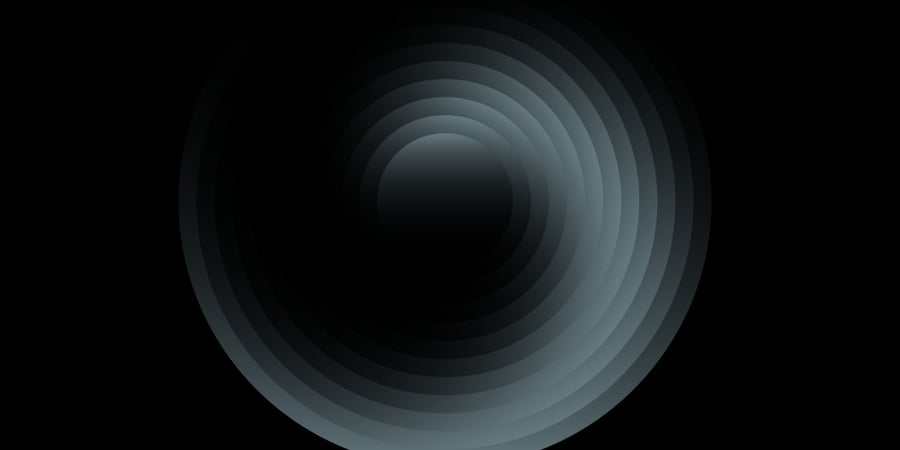