Diamond-like carbon (DLC) coatings blend the best qualities of graphite and diamond, both naturally occurring carbon forms. DLC coatings can be quite hard, lubricious, and chemically inert, making them excellent for various applications. For example, DLC coatings enable razors to provide a smooth, close shave day after day and boost performance in racing motorcycles and cars. Some DLC coatings' dark, glossy, neutral colors are visually striking. DLC-coated watches are an example. DLC coatings are applied using plasma processes (more about that below). But first:
1. What is diamond-like carbon (DLC)?
Although both graphite and diamond are made only of carbon, you can hardly find materials with more distinct properties. The reason behind those differences is their structure—how carbon atoms interconnect.
Graphite consists of strongly bonded sheets connected “loosely” between the layers. Diamonds, on the other hand, have carbon atoms connected in a strong, rigid three-dimensional structure. Consequently, graphite works well as a solid lubricant because the stiff, paper-thin layers slide easily against one another. In contrast, the tightly packed, crystalline structure of diamonds produces a form of carbon with the highest hardness and thermal conductivity of any natural material.
2. Why use plasma processes for DLC coatings?
DLC coatings are deposited by plasma processes such as PECVD. Chemical vapor deposition (CVD) is a technology for growing thin films on multiple surfaces using a chemical reaction between gas molecules. Some form of energy is needed to excite, break down, and charge the gas molecules. In turn, these react chemically with each other and a surface to “grow” a coating.
CVD can deposit various materials, from metals to plastics to ceramics to glass. The energy driving the reactions comes from heat (thermal CVD) or plasma enhancement (PECVD). Thermal CVD is usually applied near atmospheric pressure, while plasma-enhanced CVD is often a vacuum process (we use PECVD in our VaporTech® coating systems). A significant advantage of PECVD is that high temperatures are not required, enabling deposition on temperature-sensitive materials such as low-melting-point metals and alloys. A soft, elastic polymer coating will change into a hard, smooth DLC coating by simply varying the energy of the plasma during the PECVD process.
3. Does DLC create hard or lubricious coatings?
A DLC coating is amorphous, like glass, with bonding ranging from mostly graphite-like to more diamond-like. The ability to tailor how the carbon atoms interconnect by changing process parameters allows us to produce materials approaching the hardness of natural diamond. However, there are tradeoffs, harder coatings tend to be more highly stressed, so the adhesion layer (the layer between the DLC coating and the surface) is crucial.DLC coating adheres well to the surface when the adhesion layer is optimal. In some applications, a softer but tougher coating will be more durable than a hard, stressed coating. In either case, lubricity helps lower the rate of wear.
The exceptional combination of DLC coatings’ lubricity and hardness means we can tailor these coatings for many applications. For example:
- DLC coatings enhance fuel efficiency and boost horsepower by reducing sliding friction and wear on performance engine components like injectors and camshaft bearings.
- DLC coatings ease release and enhance the lifetime of molds in injection molding of plastics.
- Some DLC coatings' dark, glossy, neutral colors are visually striking and add decorative characteristics to their functional properties.
We hope you enjoyed our answers to your DLC coating questions. Let VaporTech help determine if DLC coatings will add value to your products. Contact us today!
Recent posts
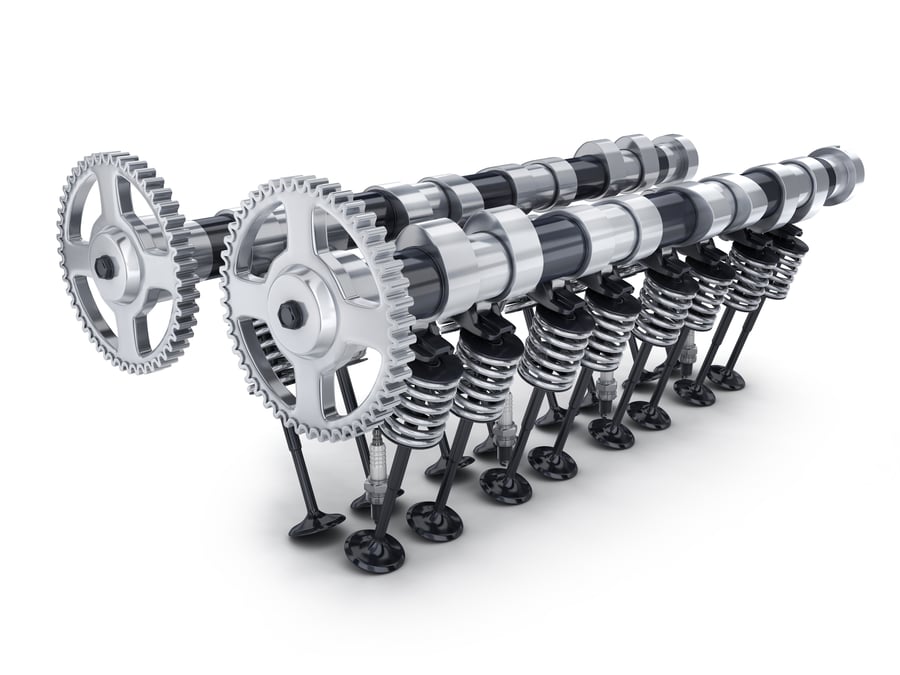
What is DLC, Also Known as Diamond-Like-Carbon Coating?
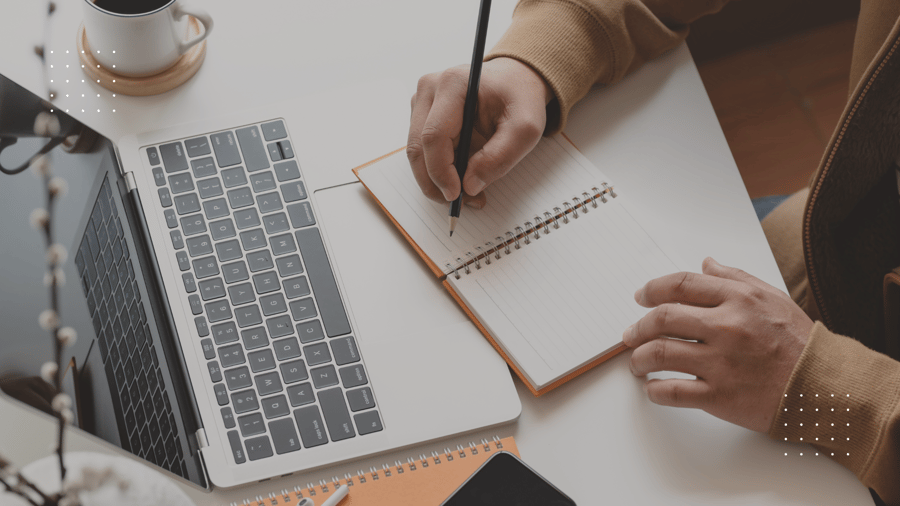
Learn More About PVD Coatings by Watching Our Webinar Presentations
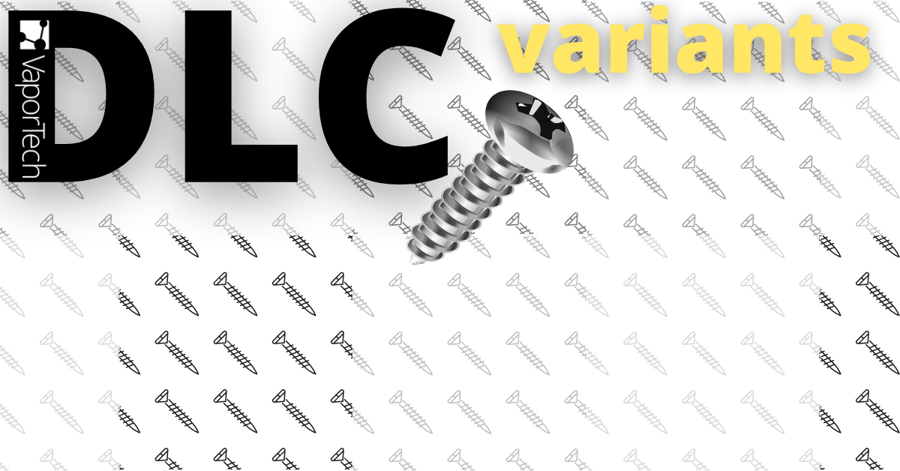