PVD Colors: How to Ensure Beautiful, Consistent Colors


Appearance and function define most consumer products, ranging from faucets to automobiles. However, the appearance of a product can be challenging to communicate and assess. First, the finishing industry has a vast and inconsistent vocabulary for defining PVD colors. Color is subjective even when everyone is on the same wavelength with the terminology. One person’s yellow-gold might be another person’s school bus yellow. The perception of color can also drastically change with lighting, like when you view a product under fluorescent, daylight, or incandescent light.
To further complicate things, 10% of the population has some degree of color blindness. Disparities between observers’ perceptions, the sample’s orientation, and changes in general lighting conditions can lead to inconsistent perceptions of color. So, as a PVD coating machine manufacturer providing optimized finishes to fit your needs, how do we create beautiful, consistent colors?
Color challenges in manufacturing
These challenges in quantifying PVD color lead to challenges in manufacturing products. The final product must often meet a specific uniform color target. Achieving uniformity can be especially difficult for products made of multiple pieces (for example, appliances and mobile electronics), which are often manufactured at different facilities or on different equipment.
Color assessment
As previously mentioned, lighting influences color perception. Natural daylight can produce smooth, vibrant colors, while fluorescent lights tend to bring out a specific color, depending on the bulb’s color temperature. Therefore, lighting, including the surroundings that influence reflected light, must be consistent when quantifying color. Trained, qualified inspectors must visually assess color uniformity under controlled lighting conditions. The inspectors’ vision should be qualified with a standard color vision test because color blindness is so prevalent.
Texture and orientation also influence color perception. Polished surfaces often appear darker than textured surfaces of the same color because the eye ignores a shiny surface’s highly reflective specular reflections when judging appearance. The orientation of light sources changes the perception of color. For example, light sources around a kitchen reflect off the surface angles of a faucet, producing an appearance that changes with viewpoint.
Using color measurement instruments
To quantify color, using a color measurement instrument can sometimes complement or even replace visual inspection for color. Instruments like spectrophotometers can remove the subjectivity out of color measurement. They make it easy to define the color and intensity of the light source. The orientation of the surface relative to the light source and the detector can all be well-defined. A color-measurement instrument can quantify color in a defined “color space.” For example, color is quantified by values for lightness (L*), green to red (a*), and blue to yellow (b*) in the CIELAB color space. These values of L*, a*, and b* were designed to correlate with perceived visual changes in color.
Relying on the human eye
These tools are helpful, but in the end, people still need control over the PVD coating, particularly with complex three-dimensional products. For example, light reflected at shallow angles from curved surfaces can escape from the input aperture of a spectrophotometer undetected, which will at least influence the L* or lightness value.
Manufacturing products with an attractive, uniform look typically requires a well-defined quality control process that often combines the human eye and color measurement instruments. For more information about PVD color options and development and the PVD systems that produce them, call us at (303) 652-8500.
Recent posts
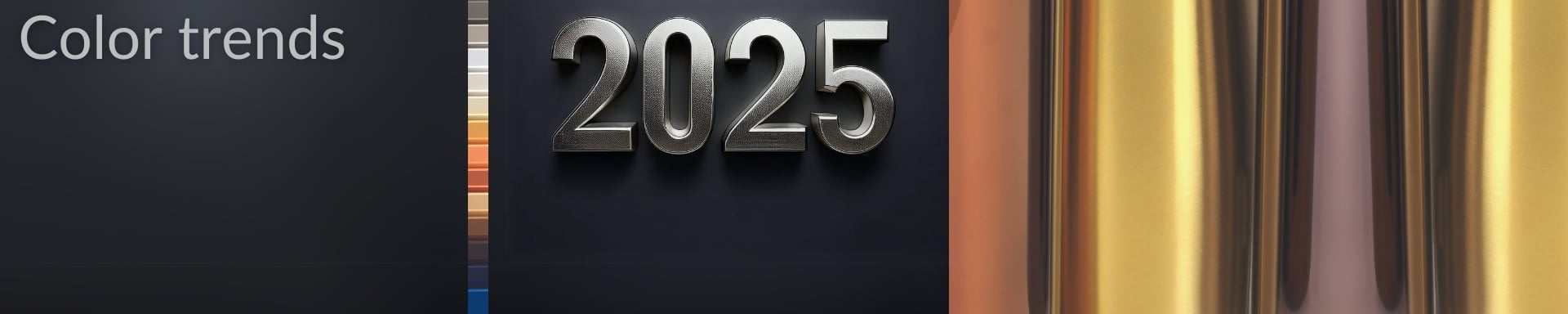
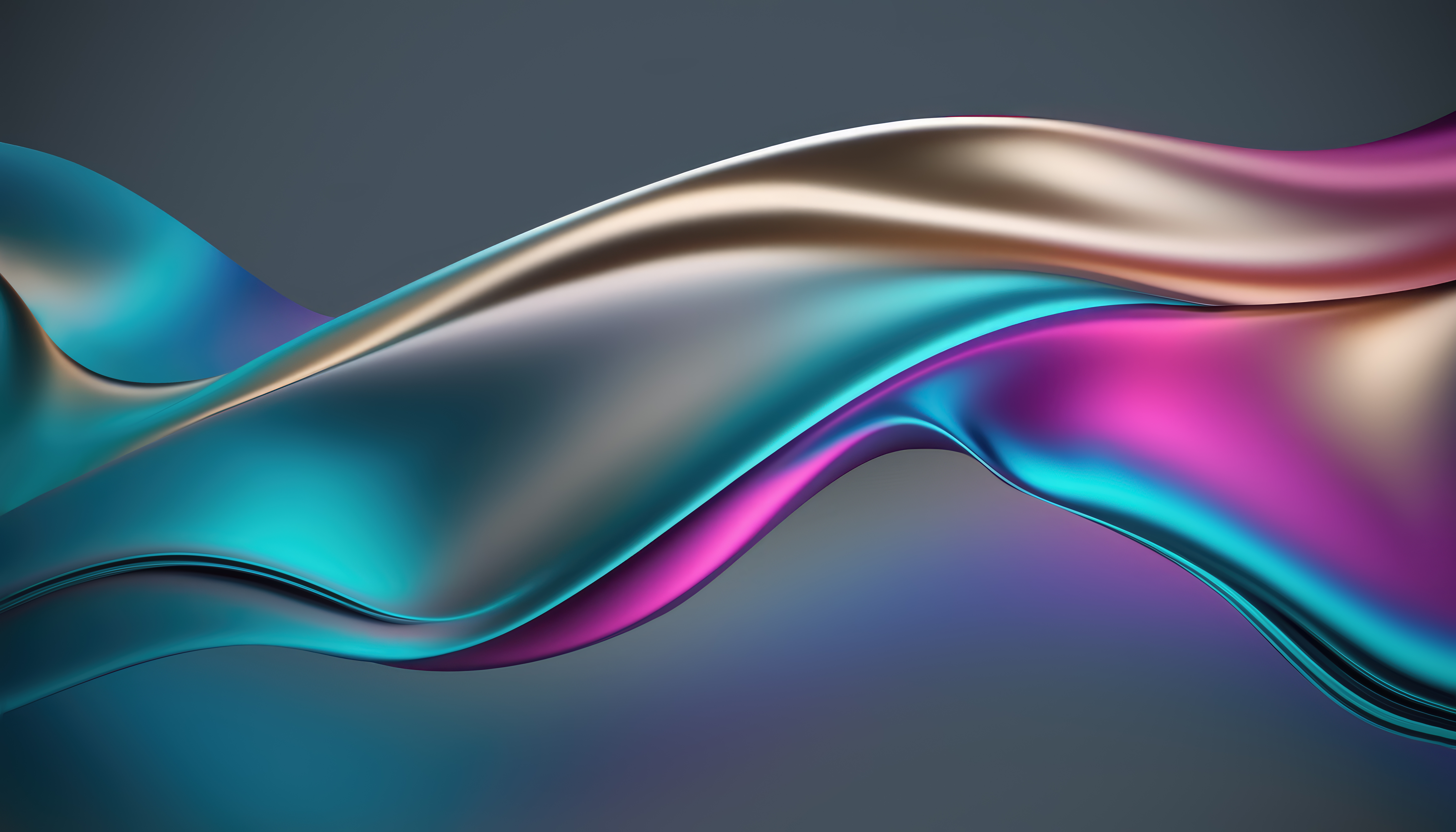
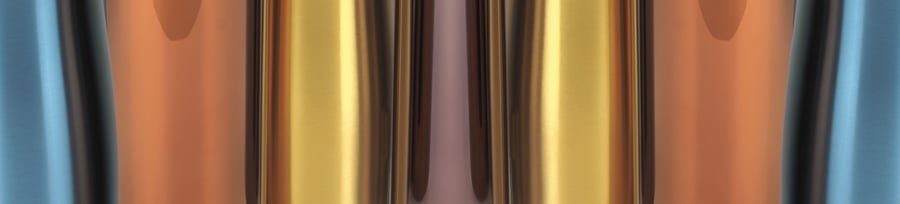
What is PVD coating used for?
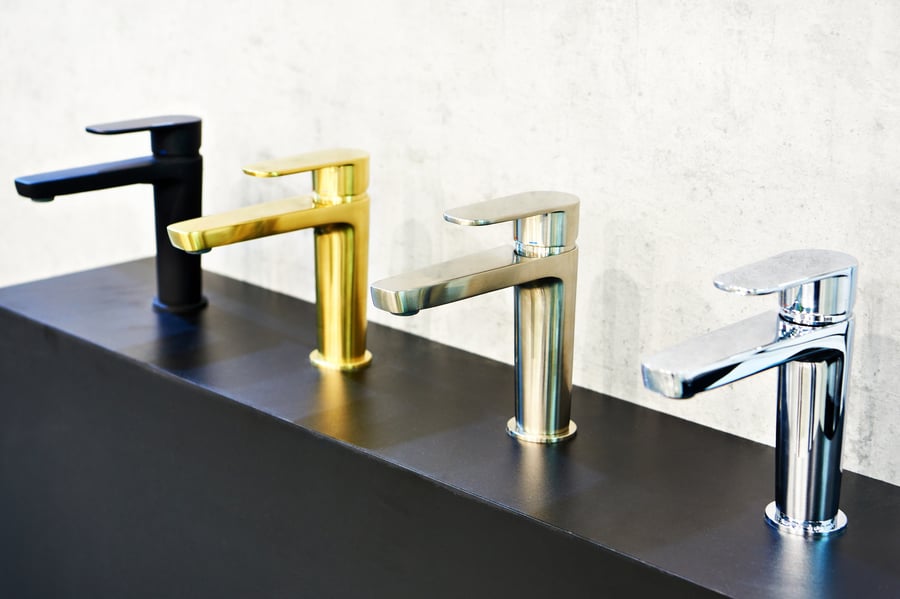
PVD Coating Durability: Does PVD Coating Wear Off, and How Durable is PVD Coating for My Product?
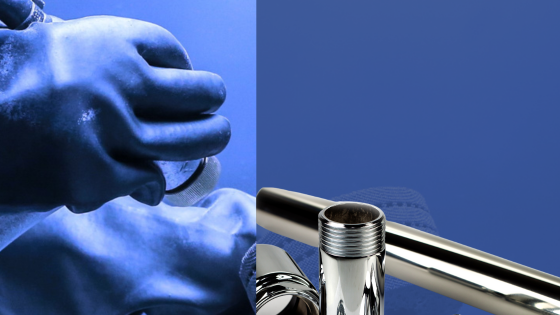